Demagging and manganese reducing phosphorus direct-reverse flotation technology of low-grade manganic phosphorite ore
A technology of reducing manganese and phosphorus with magnesium, positive and negative flotation, applied in flotation, solid separation, etc., can solve problems such as uneconomical, high content of MgO and MnO impurities in phosphorus concentrate, difficulty in removing harmful impurities of magnesium and manganese, and achieve effective Sorting and improving the effect of beneficiation recovery
- Summary
- Abstract
- Description
- Claims
- Application Information
AI Technical Summary
Problems solved by technology
Method used
Image
Examples
Embodiment 1
[0027] A low-grade manganese phosphorite ore process for removing magnesium and reducing manganese and phosphorus. The phosphorus forward flotation process includes: crushing and grinding low-grade manganese phosphorite ore to obtain Ore pulp, fineness -0.074mm accounts for 68%, control the temperature of the ore pulp at 40°C, add soda ash regulator to the ore pulp to adjust the pH value of the ore pulp to 9.8, add water glass (the amount of water glass is 1.0kg / t relative to the amount of raw ore ), then add sodium stearate (the addition of sodium stearate is 0.9kg / t relative to the amount of raw ore) and foaming agent sodium alkylbenzene sulfonate (the addition of foaming agent alkylbenzene sulfonate is relatively When the raw ore amount is 0.8kg / t), mix, stir and adjust slurry and utilize flotation machine to carry out aerated flotation, the foam product obtained is phosphorus coarse concentrate, and phosphorus coarse concentrate can be further selected (the further refined ...
Embodiment 2
[0030] A low-grade manganese apatite ore process for removing magnesium and manganese and phosphorus. The phosphorus positive flotation process includes: crushing and grinding the low-grade manganese apatite ore to obtain Ore pulp, fineness -0.074mm accounts for 65%, control the temperature of the ore pulp at 40°C, add soda ash regulator to the ore pulp to adjust the pH value of the ore pulp to 9.2, add water glass (the amount of water glass added is 0.7kg / t relative to the amount of raw ore ), then add sodium linoleate (the addition of sodium linoleate is 1.0kg / t relative to the amount of raw ore) and foaming agent triethyl-hydrogensilane (the addition of foaming agent triethyl-hydrogensilane is relatively When the raw ore amount is 0.7kg / t), mix, stir and adjust slurry and utilize flotation machine to carry out aerated flotation, the foam product obtained is phosphorus coarse concentrate, and phosphorus coarse concentrate can be further selected (the further refined The addi...
Embodiment 3
[0033] A low-grade manganese phosphorite ore process for removing magnesium and reducing manganese and phosphorus. The phosphorus forward flotation process includes: crushing and grinding low-grade manganese phosphorite ore to obtain Ore pulp, fineness -0.074mm accounts for 68%, control the temperature of the ore pulp at 40°C, add soda ash regulator to the ore pulp to adjust the pH value of the ore pulp to 9.8, add water glass (the amount of water glass is 1.0kg / t relative to the amount of raw ore ), then add sodium ricinoleate (the addition of sodium ricinoleate is 1.0kg / t relative to the amount of raw ore) and foaming agent polyethylene glycol ether (the addition of foaming agent polyethylene glycol ether is relative to the amount of raw ore amount is 0.6kg / t) to mix, stir slurry and utilize flotation machine to carry out aerated flotation, the foam product that obtains is phosphorus coarse concentrate, and phosphorus coarse concentrate can further be selected (the described ...
PUM
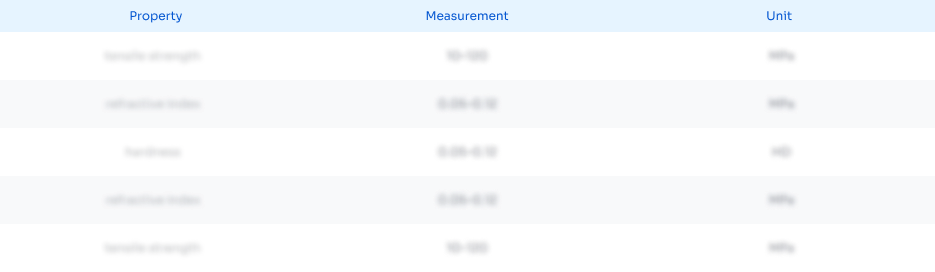
Abstract
Description
Claims
Application Information

- Generate Ideas
- Intellectual Property
- Life Sciences
- Materials
- Tech Scout
- Unparalleled Data Quality
- Higher Quality Content
- 60% Fewer Hallucinations
Browse by: Latest US Patents, China's latest patents, Technical Efficacy Thesaurus, Application Domain, Technology Topic, Popular Technical Reports.
© 2025 PatSnap. All rights reserved.Legal|Privacy policy|Modern Slavery Act Transparency Statement|Sitemap|About US| Contact US: help@patsnap.com