Mineral separation process of complex fluorite difficult to separate
A fluorite ore, refractory technology, applied in flotation, solid separation and other directions, can solve the problems of large amount of mineral processing chemicals, high energy consumption, many types, etc., to achieve efficient development and utilization, high mineral processing recovery rate, strengthen inhibition effect Effect
- Summary
- Abstract
- Description
- Claims
- Application Information
AI Technical Summary
Problems solved by technology
Method used
Image
Examples
Embodiment 1
[0041] According to the mass ratio of 1:340, sodium hydroxide and water were respectively taken to form a sodium hydroxide solution, and steam was introduced to raise the temperature of the sodium hydroxide solution to 100°C, and 1 kg of sodium hydroxide solution was added to 53 kg of sodium hydroxide solution. The ratio of oleic acid is to add oleic acid to the sodium hydroxide solution after heating, and stir for 30 minutes to make the reaction fully proceed. During the process of adding oleic acid to the sodium hydroxide solution and stirring, continue to feed steam to keep the reaction temperature constant. Keep it at 100°C. After the heating reaction is completed, stop adding steam and let it stand for 30 minutes to remove other fatty acid reactants with higher melting points floating on the upper part of the reacted liquid, and cool the reacted liquid to room temperature to obtain modified oleic acid; According to the mass ratio of 1:3, the density is 1.46g / cm 3 Add sodi...
Embodiment 2
[0052] According to the mass ratio of 1:350, sodium hydroxide and water were respectively taken to form a sodium hydroxide solution, and steam was introduced to raise the temperature of the sodium hydroxide solution to 90°C, and 1 kg of sodium hydroxide solution was added to 53 kg of sodium hydroxide solution. The ratio of oleic acid is to add oleic acid to the sodium hydroxide solution after heating, and stir for 35 minutes to make the reaction fully proceed. During the process of adding oleic acid to the sodium hydroxide solution and stirring, continue to feed steam to keep the reaction temperature constant. Keep it at 90°C. After the heating reaction is completed, stop steaming and let it stand for 40 minutes to remove other fatty acid reactants with higher melting points floating on the upper part of the reacted liquid. Cool the reacted liquid to room temperature to obtain modified oleic acid. ;According to the mass ratio of 1:3.5, the density is 1.46g / cm 3 Add sodium wate...
Embodiment 3
[0058] According to the mass ratio of 1:345, sodium hydroxide and water were respectively taken to form a sodium hydroxide solution, and steam was introduced to raise the temperature of the sodium hydroxide solution to 95°C, and 1 kg of sodium hydroxide solution was added to 53 kg of sodium hydroxide solution. The ratio of oleic acid is to add oleic acid to the sodium hydroxide solution after heating, and stir for 32 minutes to make the reaction fully proceed. During the process of adding oleic acid to the sodium hydroxide solution and stirring, continue to feed steam to keep the reaction temperature constant. Keep it at 95°C. After the heating reaction is completed, stop steaming and let it stand for 50 minutes to remove other fatty acid reactants with higher melting points floating on the upper part of the reacted liquid. Cool the reacted liquid to room temperature to obtain modified oleic acid. ;According to the mass ratio of 1:3.25, the density is 1.46g / cm 3 The sodium wat...
PUM
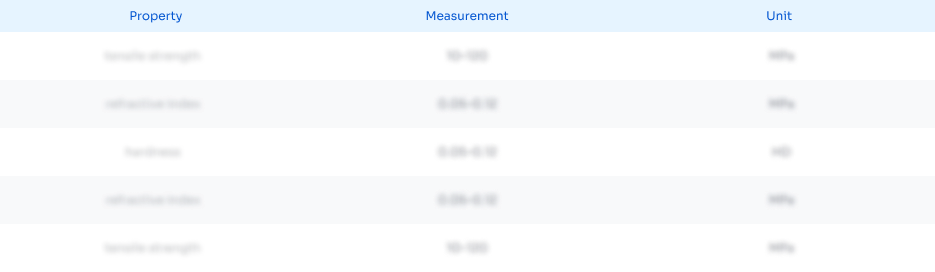
Abstract
Description
Claims
Application Information

- Generate Ideas
- Intellectual Property
- Life Sciences
- Materials
- Tech Scout
- Unparalleled Data Quality
- Higher Quality Content
- 60% Fewer Hallucinations
Browse by: Latest US Patents, China's latest patents, Technical Efficacy Thesaurus, Application Domain, Technology Topic, Popular Technical Reports.
© 2025 PatSnap. All rights reserved.Legal|Privacy policy|Modern Slavery Act Transparency Statement|Sitemap|About US| Contact US: help@patsnap.com