Method for gravity separation of fine antimony oxide ore
A technology of gravity beneficiation and antimony oxide, applied in chemical instruments and methods, wet separation, solid separation and other directions, to achieve the effects of high beneficiation recovery rate, friendly operating environment, low energy consumption and low cost
- Summary
- Abstract
- Description
- Claims
- Application Information
AI Technical Summary
Problems solved by technology
Method used
Examples
Embodiment 1
[0016] The antimony-containing low-grade flotation tailings (the mass content under the 200 mesh sieve is 56.0%, the antimony-containing grade is 1.10%, and the antimony oxidation rate is 91.0%) discharged from the production of a mineral processing site is firstly treated with high-frequency The vibrating screen removes the coarse-grained material with a fineness of 200 mesh, and then the hydrocyclone removes the sludge with a fineness of 800 mesh, and finally the material flows into the DSLXZ-4000 type suspension vibrating cone concentrator. With a processing capacity of 560kg / h, a rotation frequency of 10Hz and a vibration frequency of 20Hz, a separation is performed to obtain antimony concentrate and final tailings.
[0017] The beneficiation recovery rate is 49.25%, and the grade of antimony concentrate is 15.0%.
Embodiment 2
[0019] The tailings stockpiled in the tailings pool of a certain antimony ore dressing plant (the mass content under the 200-mesh sieve is 65.0%, the antimony grade is 0.65%, and the antimony oxidation rate is 86.0%), first use a high-frequency vibrating screen Screen out the coarse-grained material on the sieve with a fineness of 200 mesh, and then remove the slime from the sieve with a fineness of 800 mesh by a hydrocyclone, and finally the material flows into the DSLXZ-4000 type suspension vibrating cone concentrator. The processing capacity of the table is 710kg / h, the rotation frequency is 10Hz, and the vibration frequency is 18Hz, and a separation is performed to obtain antimony concentrate and final tailings.
[0020] The beneficiation recovery rate is 47.65%, and the grade of antimony concentrate is 20.0%.
Embodiment 3
[0022] The tailings discharged from a flotation plant of antimony sulfide ore (the mass content under the 200-mesh sieve is 62.0%, the antimony grade is 0.30%, and the antimony oxidation rate is 88.0%) is first screened out with a high-frequency vibrating screen Coarse-grained materials with a fineness of 200 mesh on the sieve, and then the hydrocyclone removes the slime of the sieve with a fineness of 800 mesh, and finally the material flows into the DSLXZ-4000 type suspension vibrating cone concentrator, and is processed in each machine. The amount is 690kg / h, the rotation frequency is 10Hz, and the vibration frequency is 18Hz, and a separation is carried out to obtain antimony concentrate and final tailings.
[0023] The beneficiation recovery rate is 43.65%, and the grade of antimony concentrate is 18.0%.
PUM
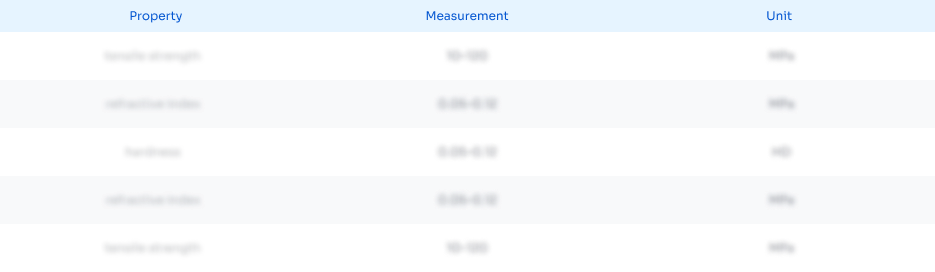
Abstract
Description
Claims
Application Information

- R&D
- Intellectual Property
- Life Sciences
- Materials
- Tech Scout
- Unparalleled Data Quality
- Higher Quality Content
- 60% Fewer Hallucinations
Browse by: Latest US Patents, China's latest patents, Technical Efficacy Thesaurus, Application Domain, Technology Topic, Popular Technical Reports.
© 2025 PatSnap. All rights reserved.Legal|Privacy policy|Modern Slavery Act Transparency Statement|Sitemap|About US| Contact US: help@patsnap.com