A Tracking Method for Robot Constant Force Surface Based on Fuzzy Iterative Algorithm
An iterative algorithm and robot technology, applied in manipulators, program-controlled manipulators, manufacturing tools, etc., can solve problems such as staying in simulation, inaccurate surface contours, and unstable contact force between robots and surfaces, and achieve simple results.
- Summary
- Abstract
- Description
- Claims
- Application Information
AI Technical Summary
Problems solved by technology
Method used
Image
Examples
Embodiment 1
[0040] A robot constant force surface tracking method based on fuzzy iterative algorithm. The method is based on a robot constant force tracking platform, including a six-axis industrial robot, a workbench, a curved surface workpiece, a six-dimensional force sensor, a host computer, and a data acquisition module. The robot always moves along the x direction at a constant speed. When the robot is in contact with the workpiece, it shifts along the y direction according to the magnitude of the force, and tracks along the unknown surface to ensure that the end of the robot does not leave the curved workpiece.
[0041] Specifically include the following steps:
[0042] (1) Establish the mapping relationship between the surface normal force and the known sensor coordinate system;
[0043] (2) Tracking along the unknown surface, the initial control algorithm is the PD algorithm, and the initial trajectory and force parameters are obtained;
[0044] (3) Obtain the trajectory and forc...
PUM
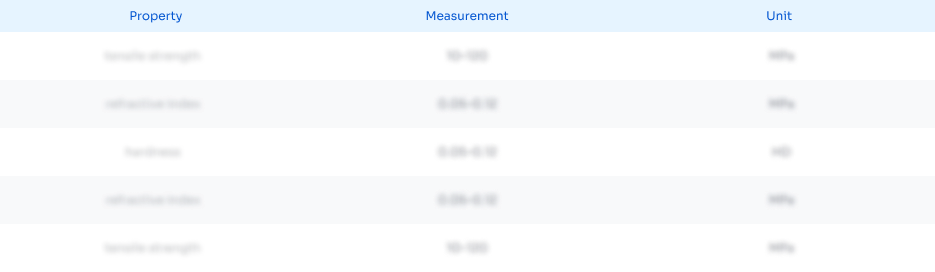
Abstract
Description
Claims
Application Information

- R&D Engineer
- R&D Manager
- IP Professional
- Industry Leading Data Capabilities
- Powerful AI technology
- Patent DNA Extraction
Browse by: Latest US Patents, China's latest patents, Technical Efficacy Thesaurus, Application Domain, Technology Topic, Popular Technical Reports.
© 2024 PatSnap. All rights reserved.Legal|Privacy policy|Modern Slavery Act Transparency Statement|Sitemap|About US| Contact US: help@patsnap.com