Aluminum electrolyzing technology
A technology of electrolytic aluminum and process, applied in the field of electrolytic aluminum process, can solve the problems of primary crystal temperature containing carbon slag, achieve the effect of reducing primary crystal temperature, reducing cost, and facilitating separation
- Summary
- Abstract
- Description
- Claims
- Application Information
AI Technical Summary
Problems solved by technology
Method used
Examples
Embodiment 1
[0023] A kind of electrolytic aluminum process, comprises the following steps:
[0024] A. Mix electrolytes other than alumina, cryolite is used as a solvent for electrolytic reaction alumina, dissolve alumina in cryolite, heat the electrolyte mixture except alumina until it is molten, and then add ice crystals containing alumina The molten rock solution is obtained, and the electrolyte is dried in an oven before mixing. The composition of the electrolyte is: 3% alumina, 25% aluminum fluoride, 5% calcium fluoride, 5% magnesium fluoride, and 32% sodium fluoride. %, lithium fluoride 2%, potassium fluoride 5%, potassium fluoroaluminate 23%;
[0025] B. Connect the electrodes of the electrolytic cell to the power supply, place the melt obtained in step A in the electrolytic cell and perform electrolysis at 820°C with a current density of 1A / cm 2 , to obtain the aluminum liquid after electrolysis, in which the height of the electrolyte melt is 25cm, the superheat of the electrolyt...
Embodiment 2
[0029] A kind of electrolytic aluminum process, comprises the following steps:
[0030] A. Mix electrolytes other than alumina, cryolite is used as a solvent for electrolytic reaction alumina, dissolve alumina in cryolite, heat the electrolyte mixture except alumina until it is molten, and then add ice crystals containing alumina The molten rock solution is obtained, and the electrolyte is dried in an oven before mixing. The composition of the electrolyte is: 6% alumina, 25% aluminum fluoride, 2% calcium fluoride, 2% magnesium fluoride, and 35% sodium fluoride. %, lithium fluoride 3%, potassium fluoride 2%, potassium fluoroaluminate 25%;
[0031] B. Connect the electrodes of the electrolytic cell to the power supply, place the melt obtained in step A in the electrolytic cell and perform electrolysis at 820°C with a current density of 1A / cm 2 , to obtain the aluminum liquid after electrolysis, in which the height of the electrolyte melt is 20cm, the superheat of the electrolyt...
Embodiment 3
[0035] A kind of electrolytic aluminum process, comprises the following steps:
[0036] A. Mix electrolytes other than alumina, cryolite is used as a solvent for electrolytic reaction alumina, dissolve alumina in cryolite, heat the electrolyte mixture except alumina until it is molten, and then add ice crystals containing alumina The molten rock solution is obtained, and the electrolyte is dried in an oven before mixing. The composition of the electrolyte is: 3% alumina, 30% aluminum fluoride, 2% calcium fluoride, 3% magnesium fluoride, and 35% sodium fluoride. %, lithium fluoride 5%, potassium fluoride 2%, potassium fluoroaluminate 20%;
[0037] B. Connect the electrodes of the electrolytic cell to the power supply, place the melt obtained in step A in the electrolytic cell and perform electrolysis at 820°C with a current density of 1A / cm 2 , to obtain the aluminum liquid after electrolysis, in which the height of the electrolyte melt is 20cm, the superheat of the electrolyt...
PUM
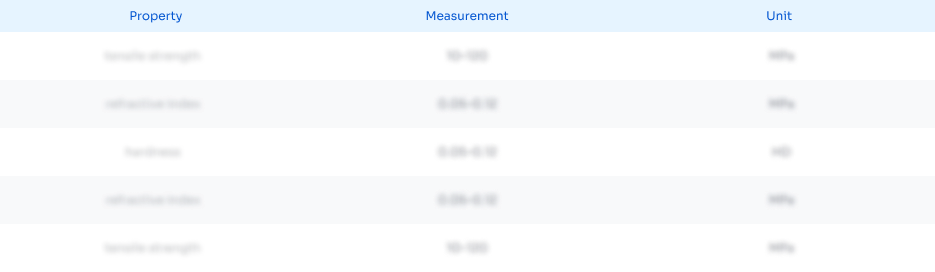
Abstract
Description
Claims
Application Information

- R&D
- Intellectual Property
- Life Sciences
- Materials
- Tech Scout
- Unparalleled Data Quality
- Higher Quality Content
- 60% Fewer Hallucinations
Browse by: Latest US Patents, China's latest patents, Technical Efficacy Thesaurus, Application Domain, Technology Topic, Popular Technical Reports.
© 2025 PatSnap. All rights reserved.Legal|Privacy policy|Modern Slavery Act Transparency Statement|Sitemap|About US| Contact US: help@patsnap.com