Ultra-high performance concrete with micro-expansion and compensation shrinkage and preparation method thereof
An ultra-high performance, shrinkage compensation technology, applied in the field of building materials, can solve the problem of inability to fully compensate for shrinkage and achieve micro-expansion, and achieve the effect of avoiding the risk of cracking, excellent working performance, and improving strength
- Summary
- Abstract
- Description
- Claims
- Application Information
AI Technical Summary
Problems solved by technology
Method used
Image
Examples
Embodiment 1
[0041] A method for preparing micro-expansion-compensated shrinkage ultra-high performance concrete, comprising the steps of:
[0042] 1) Prepare the raw materials according to the following seven different ratios:
[0043] A0 is the blank group, the ingredients are cement, fly ash, silica fume, mineral powder, quartz powder, quartz sand, water reducing agent, steel fiber and water; 1 part of cement, 0.05-0.2 parts of fly ash, 0.2- 0.5 parts, 0.1 to 0.25 parts of mineral powder, 0.05 to 0.2 parts of quartz powder, 0.9 to 1.2 parts of quartz sand, 0.01 to 0.03 parts of water reducing agent, and the volume of steel fiber is 1% to 3% of the total volume of concrete. The water-binder ratio is 0.16-0.22.
[0044] Group A1 only adds expansion agent, the ingredients are cement, fly ash, silica fume, mineral powder, quartz powder, quartz sand, expansion agent, water reducing agent, steel fiber and water; 1 part of cement, 0.05-0.2 part of fly ash , 0.2-0.5 parts of silica fume, 0.1-...
PUM
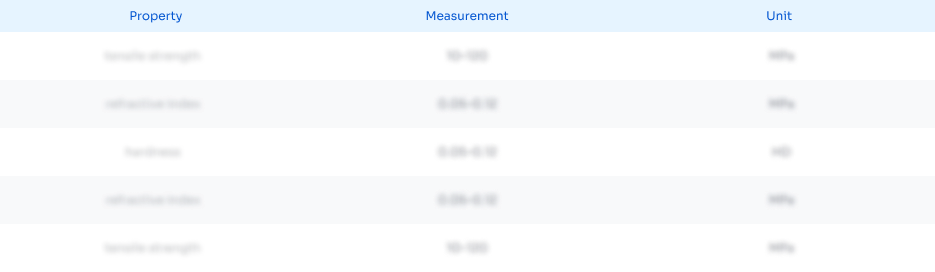
Abstract
Description
Claims
Application Information

- R&D Engineer
- R&D Manager
- IP Professional
- Industry Leading Data Capabilities
- Powerful AI technology
- Patent DNA Extraction
Browse by: Latest US Patents, China's latest patents, Technical Efficacy Thesaurus, Application Domain, Technology Topic, Popular Technical Reports.
© 2024 PatSnap. All rights reserved.Legal|Privacy policy|Modern Slavery Act Transparency Statement|Sitemap|About US| Contact US: help@patsnap.com