Method of separating and recycling SiO2 and ammonium fluorosilicate from fluorine-containing dust
A technology of silicon dioxide and ammonium fluorosilicate, applied in the directions of silicon dioxide, silicon oxide, fluorosilicic acid, etc., can solve the problems of high processing cost, difficult separation and recovery of valuable components, secondary pollution, etc., and achieve the production process. Simple process, reduce evaporation of solution, reduce the effect of waste liquid treatment
- Summary
- Abstract
- Description
- Claims
- Application Information
AI Technical Summary
Problems solved by technology
Method used
Examples
Embodiment 1
[0029] Take a batch of CVD fluorine-containing dust, measure 3 parts with whiteness lower than 80%, and 7 parts with whiteness ≥ 80%, which are regarded as two types.
[0030] First, add the two types of fluorine-containing dust obtained in the above step into different leaching tanks separately, heat water to dissolve, control the leaching liquid-solid ratio to 1:2, heat the solution to 90°C during the process, and fully stir and leaching for 2 hours.
[0031] Next, filter the leach slurry obtained in the above step while it is hot or press filter, and separate the leachate and filter residue.
[0032] Again, mix the leaching solution obtained in the above step, and put it into the crystallization reactor to cool and crystallize. The cooling crystallization temperature is 40°C. After sufficient crystallization, separate the crystal and the crystallization mother liquor.
[0033] Then, repeat the above steps for secondary leaching and secondary crystallization, the leaching li...
Embodiment 2
[0036] Take a batch of CVD fluorine-containing dust, measure 2 parts with whiteness lower than 80%, and 8 parts with whiteness ≥ 80%, which are regarded as two types.
[0037] First, add the two types of fluorine-containing dust obtained in the previous step into separate leaching tanks, add ammonium fluorosilicate crystallization mother liquor (20°C crystallization mother liquor) to dissolve, control the ratio of leaching liquid to solid to 1:5, and heat during the process Solution to 60 ° C, fully stirred and leached for 1h.
[0038] Next, filter the leach slurry obtained in the above step while it is hot or press filter, and separate the leachate and filter residue.
[0039] Again, mix the net filtrate obtained in the above step, and add it to the crystallization reactor for cooling and crystallization. The cooling crystallization temperature is 20°C. After sufficient crystallization, separate the crystals and the crystallization mother liquor.
[0040] Then, repeat the ab...
PUM
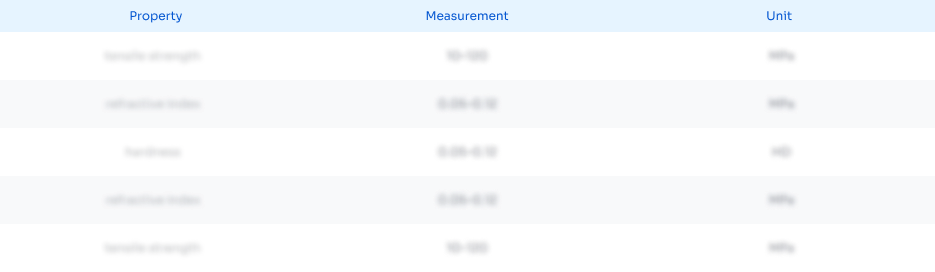
Abstract
Description
Claims
Application Information

- R&D Engineer
- R&D Manager
- IP Professional
- Industry Leading Data Capabilities
- Powerful AI technology
- Patent DNA Extraction
Browse by: Latest US Patents, China's latest patents, Technical Efficacy Thesaurus, Application Domain, Technology Topic, Popular Technical Reports.
© 2024 PatSnap. All rights reserved.Legal|Privacy policy|Modern Slavery Act Transparency Statement|Sitemap|About US| Contact US: help@patsnap.com