A Second-Order Nonlinear Energy Trap for Suppressing Rotor System Vibration
A nonlinear energy well and rotor technology, applied in the direction of rotation vibration suppression, vibration suppression adjustment, spring/shock absorber, etc., can solve the problems of large application limitations, narrow vibration suppression frequency band, complex structure, etc., and achieve variable parameters , Enhanced vibration suppression effect and increased flexibility
- Summary
- Abstract
- Description
- Claims
- Application Information
AI Technical Summary
Problems solved by technology
Method used
Image
Examples
Embodiment Construction
[0031] Attached below Figure 1-10 , and give examples to further describe in detail the secondary nonlinear energy well for vibration suppression of the rotor system of the present invention.
[0032] The disk 9 and the shaft 17 are assembled into a rotor system, and the shaft 17 is fixed on the outer frame 18 through the shaft end support 19;
[0033] The support assembly includes a bearing 8, a support disc 10 and a shaft sleeve 11. The bearing 8 is fixed in the support disc 10. The function of the shaft sleeve 11 is to prevent the axial movement of the nonlinear energy well body. The support disc 10 passes through the primary connection assembly Connect with the primary vibrator-absorbing mass block 15;
[0034] The connecting holes on the inner circumference of the first-level vibrator-absorbing mass block 15 are matched and connected with the two first-level connecting rods 12; the gap holes and the four first-level segmented linear rods 13 form clearance fits; the hole...
PUM
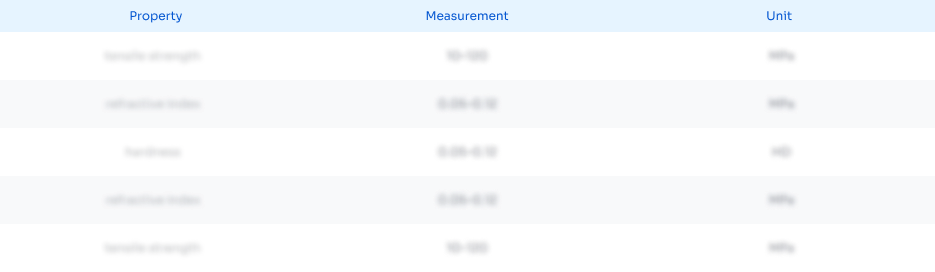
Abstract
Description
Claims
Application Information

- Generate Ideas
- Intellectual Property
- Life Sciences
- Materials
- Tech Scout
- Unparalleled Data Quality
- Higher Quality Content
- 60% Fewer Hallucinations
Browse by: Latest US Patents, China's latest patents, Technical Efficacy Thesaurus, Application Domain, Technology Topic, Popular Technical Reports.
© 2025 PatSnap. All rights reserved.Legal|Privacy policy|Modern Slavery Act Transparency Statement|Sitemap|About US| Contact US: help@patsnap.com