Experimental coiled tubing fracturing tool positioning error measurement system and method
A technology of positioning error and measurement system, applied in the direction of measurement, drill pipe, casing, etc., can solve the problems of lack of direct observation and measurement error, low accuracy, etc., to achieve reasonable design, improve operation efficiency and accuracy high effect
- Summary
- Abstract
- Description
- Claims
- Application Information
AI Technical Summary
Problems solved by technology
Method used
Image
Examples
Embodiment 1
[0038] In order to overcome the lack of an intuitive measurement method for coiled tubing fracturing tool positioning error in the prior art, the existing positioning error measurement method has low accuracy, and the actions of the existing positioning measurement system are all judged by the load signal or electromagnetic signal transmitted to the ground , can not directly observe and measure the problem of the error between the actual spray point and the theoretical spray point, the present invention provides such as Figure 1-4 The described system and method for measuring the positioning error of a coiled tubing fracturing tool for experiments has a reasonable design and high precision, and the experimental data truly reflects the error between the spray point of the spray gun and the design spray point, which is used for later positioning error compensation. It provides a reliable basis and has good reference significance.
[0039] One of the purposes of the present inve...
Embodiment 2
[0050] Based on the above embodiments, in this embodiment, the connector 2 and the fracturing tool 9 are connected through the safety joint 3 .
[0051] The fracturing tool 9 includes a spray gun 4, a packer 6, a positioner 7 and a guide centralizer 8; the spray gun 4, the packer 6, the positioner 7 and the guide centralizer 8 are connected in sequence.
[0052] The positioner 7 is provided with an induction block 19 .
[0053] The guide centralizer 8 at the tail of the fracturing tool 9 is connected with a soft tape 10 .
[0054] The windowing test casing 10 is connected with the short casing two 14 through the casing collar two 15 .
[0055] The second short sleeve 14 is connected to the first short sleeve 12 through the first sleeve collar 13 .
[0056] In this embodiment, the lengths of short casing one 12, short casing two 14, and windowing experimental casing 10 are designed to ensure that after short casing one 12 is connected with short casing two 14 and windowing ex...
Embodiment 3
[0060] Based on the above two embodiments, this embodiment provides image 3 with 4 A method for measuring positioning errors of coiled tubing fracturing tools for experiments, the specific measurement steps are:
[0061] Step 1: Simulate the process of the locator 7 passing through the first casing collar 13 and the second casing collar 15;
[0062] After the coiled tubing 1 is connected with the connector 2, the safety joint 3 and the fracturing tool 9, the coiled tubing 1 and the fracturing tool 9 move back and forth in the short casing 1 12, the short casing 2 14, and the windowing test casing 10, and at the same time , to verify the setting and unsealing performance of the packer 6;
[0063] Lower the fracturing tool 9, expose the sensing block 19 of the positioner 7 to the tail end of the short casing 12, lift the coiled tubing 1 at a speed of 4-5 m / min, and observe that the positioner 7 passes through the casing section collar 1 13 and casing section hoop 2 15 and th...
PUM
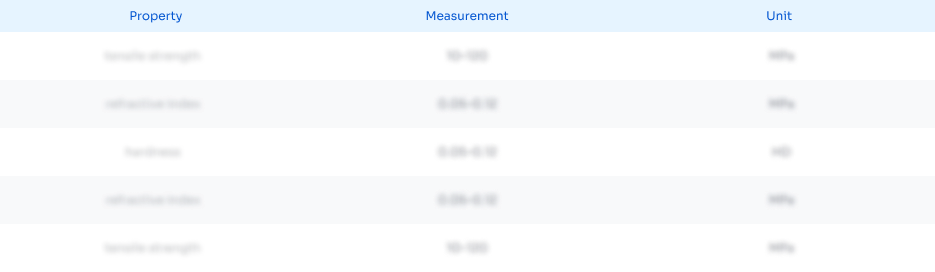
Abstract
Description
Claims
Application Information

- R&D Engineer
- R&D Manager
- IP Professional
- Industry Leading Data Capabilities
- Powerful AI technology
- Patent DNA Extraction
Browse by: Latest US Patents, China's latest patents, Technical Efficacy Thesaurus, Application Domain, Technology Topic, Popular Technical Reports.
© 2024 PatSnap. All rights reserved.Legal|Privacy policy|Modern Slavery Act Transparency Statement|Sitemap|About US| Contact US: help@patsnap.com