A kind of waste lubricating oil pretreatment method
A waste lubricating oil and pretreatment technology, which is applied in the direction of lubricating compositions, etc., can solve the problems of poor balance between additives, residual asphalt metal removal, poor metal ion removal effect, and low recycling rate of waste lubricating oil. Achieve the effects of good pretreatment effect, small impurity particles, and low initial investment in equipment
- Summary
- Abstract
- Description
- Claims
- Application Information
AI Technical Summary
Problems solved by technology
Method used
Image
Examples
Embodiment 1
[0024] Pump the waste lubricating oil into the oil tank with stirring, stir for 30 minutes, control the temperature at 80°C, and let it settle for 10 hours to remove large mechanical impurities and part of the water;
[0025] Take 100 parts of waste lubricating oil in the upper layer after settling and add it to the reaction kettle, add 1 part of complexing agent to make an aqueous solution, the complexing agent is a mixture of sulfates, amides and phosphates, constant at 90 Stir the reaction at ℃ for 30 minutes, continue to heat up to 150 ℃, stir and dehydrate for 30 minutes.
[0026] After the complexation reaction, the mixture is subjected to centrifugation and slag removal;
[0027] Take the supernatant liquid after centrifugal deslagging treatment and place it in a container for flash evaporation, take the supernatant liquid after centrifugal deslagging treatment and place it in a container for flash evaporation, gradually heat up in nitrogen atmosphere, and steam light h...
Embodiment 2
[0034] Pump the waste lubricating oil into the oil tank with stirring, stir for 30 minutes, control the temperature at 80°C, and let it settle for 10 hours to remove large mechanical impurities and part of the water;
[0035] Take 100 parts of waste lubricating oil in the upper layer after settling and add it to the reaction kettle, and add 2 parts of complexing agent to form an aqueous solution. The complexing agent is a mixture of sulfates, amides and phosphates, which is constant at 90 Stir and react at ℃ for 30 minutes, continue to heat up to 150 ℃, stir and dehydrate for 30 minutes;
[0036] After the complexation reaction, the mixture is subjected to centrifugation and slag removal;
[0037] Take the supernatant liquid after centrifugal deslag treatment and place it in a container for flash evaporation, gradually heat up in nitrogen atmosphere, and steam out light hydrocarbons, water, and gasoline in sequence, and finally control the temperature of the kettle not to exce...
Embodiment 3
[0043] Pump the waste lubricating oil into the oil tank with stirring, stir for 30 minutes, control the temperature at 80°C, and let it settle for 10 hours to remove large mechanical impurities and part of the water;
[0044] Take 100 parts of the upper layer of waste lubricating oil after settling and add it to the reaction kettle, add 1 part of complexing agent to make an aqueous solution, the complexing agent is a mixture of sulfates, amides and phosphates, and keep it at 90°C Stir and react for 30 minutes, continue to heat up to 150°C, and stir and dehydrate for 30 minutes;
[0045] After the complexation reaction, the mixture is subjected to centrifugation and slag removal;
[0046] Take the supernatant liquid after centrifugal deslag treatment and place it in a container for flash evaporation, gradually heat up in nitrogen atmosphere, and steam out light hydrocarbons, water, and gasoline in sequence, and finally control the temperature of the kettle not to exceed 200°C t...
PUM
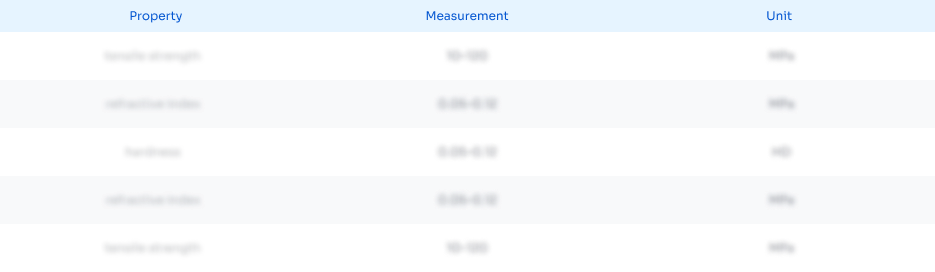
Abstract
Description
Claims
Application Information

- Generate Ideas
- Intellectual Property
- Life Sciences
- Materials
- Tech Scout
- Unparalleled Data Quality
- Higher Quality Content
- 60% Fewer Hallucinations
Browse by: Latest US Patents, China's latest patents, Technical Efficacy Thesaurus, Application Domain, Technology Topic, Popular Technical Reports.
© 2025 PatSnap. All rights reserved.Legal|Privacy policy|Modern Slavery Act Transparency Statement|Sitemap|About US| Contact US: help@patsnap.com