A kind of crystal form optimized concrete synergist mother liquor and preparation method thereof
A concrete synergist and crystal form technology, which is applied in the field of concrete synergists, can solve the problems of large impact on price, impact on concrete adaptability, and relatively large price fluctuations of alcohol amines, so as to reduce cement consumption and cost price fluctuations Small, the effect of increasing the amount of utilization
- Summary
- Abstract
- Description
- Claims
- Application Information
AI Technical Summary
Problems solved by technology
Method used
Image
Examples
Embodiment 1
[0043] 1.1 Raw materials, parts by mass,
[0044] Cement solubilizer: polymethacryloxyethyltrimethylammonium chloride aqueous solution (viscosity average molecular weight 1000, mass concentration 20%);
[0045] Supersaturation stabilizer: sodium polystyrene sulfonate aqueous solution (viscosity average molecular weight 1000, mass concentration 20%);
[0046] Hydration inducer: calcium nitrate;
[0047] Crystal form optimizer: zinc nitrate;
[0048] Defoamer: polyoxyethylene polyoxypropylene glyceryl ether.
[0049] 1.2 The preparation process is:
[0050] At 5°C, with a stirring speed of 300r / min, dissolve 0.2 parts of cement solubilizer and 0.5 parts of supersaturation stabilizer in a reactor filled with 25.05 parts of deionized water, and then add 60 parts of hydration inducer within 1 hour Add 2 parts into the reactor for complexation and dissolution, then add 4 parts of crystal form optimizer into the reactor, stir for 20 minutes, add 0.05 part of defoamer, and stir fo...
Embodiment 2
[0052] 2.1 Raw materials, parts by mass,
[0053] Cement solubilizer: polymethacryloxyethyltrimethylammonium chloride aqueous solution (viscosity average molecular weight 2000, mass concentration 20%);
[0054] Supersaturation stabilizer: sodium polyaspartate aqueous solution (viscosity average molecular weight 1500, mass concentration 20%);
[0055] Hydration inducer: calcium nitrate;
[0056] Crystal form optimizer: zinc nitrate;
[0057] Defoamer: polyoxyethylene polyoxypropylene glyceryl ether;
[0058] 2.2 The preparation process is:
[0059] At 40°C, with a stirring speed of 200r / min, 0.8 parts of cement solubilizer and 1 part of supersaturation stabilizer were dissolved in a reactor filled with 35.25 parts of deionized water, and then 65 parts of hydration inducer were dissolved in Add 4 times within 1 hour to the reactor for complexation and dissolution, then add 8 parts of crystal form optimizer to the reactor, stir for 30 minutes, add 0.15 parts of defoamer, and st...
Embodiment 3
[0061] 3.1 Raw materials, parts by mass
[0062] Cement solubilizer: polyacryloyloxyethyltrimethylammonium chloride aqueous solution (viscosity average molecular weight 1020, mass concentration 20%);
[0063] Supersaturation stabilizer: sodium polystyrene sulfonate aqueous solution (viscosity average molecular weight 1490, mass concentration 20%);
[0064] Hydration inducer: calcium nitrite;
[0065] Crystal form optimizer: ferric nitrate;
[0066] Defoamer: polyoxyethylene polyoxypropylene glyceryl ether.
[0067] 3.2 The preparation process is:
[0068] At 25°C, with a stirring speed of 250r / min, 0.3 parts of cement solubilizer and 0.9 parts of supersaturation stabilizer were dissolved in a reactor filled with 30 parts of deionized water, and then 62 parts of hydration inducer were dissolved in 1h Add 3 times into the reactor for complexation and dissolution, then add 5 parts of crystal form optimizer into the reactor, stir for 25 minutes, add 0.1 part of defoamer, and s...
PUM
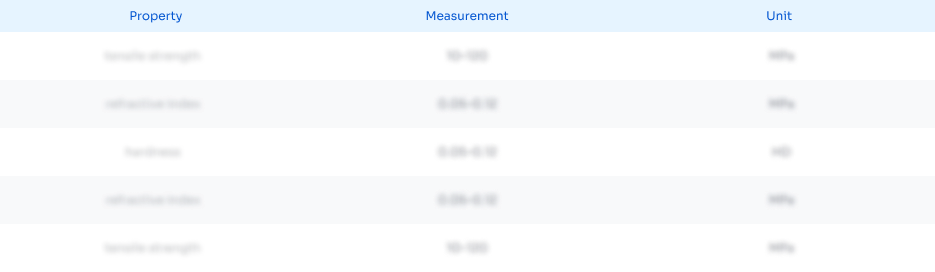
Abstract
Description
Claims
Application Information

- R&D Engineer
- R&D Manager
- IP Professional
- Industry Leading Data Capabilities
- Powerful AI technology
- Patent DNA Extraction
Browse by: Latest US Patents, China's latest patents, Technical Efficacy Thesaurus, Application Domain, Technology Topic, Popular Technical Reports.
© 2024 PatSnap. All rights reserved.Legal|Privacy policy|Modern Slavery Act Transparency Statement|Sitemap|About US| Contact US: help@patsnap.com