Manufacturing formula and manufacturing process for marble textures
A production process and marble technology, which is applied in the field of marble texture, can solve the problems of not perfectly reflecting the natural texture of marble texture, monolithic texture effect, and many processing procedures, so as to achieve high degree of naturalness, simplification of labor, and good natural agility Effect
- Summary
- Abstract
- Description
- Claims
- Application Information
AI Technical Summary
Problems solved by technology
Method used
Examples
Embodiment 1
[0023] A formula for making marble texture, which includes: 97.99% polylaurolactam, 0.01% toner, and 2% masterbatch, wherein the masterbatch includes: 60% polylaurolactam, titanium dioxide 38% and pigment 2%.
[0024] The production process of the marble texture includes:
[0025] Step 1, mixing and grinding the above-mentioned polylaurolactam, titanium dioxide and pigment to form a masterbatch;
[0026] Step 2, stirring and mixing the polylaurolactam, toner, and color masterbatch in the amount of the above formula;
[0027] Step 3, putting the mixture into a dehumidifier for drying; the drying temperature of the dehumidifier is 100°C. The drying time is 6 hours.
[0028] Step 4, put the dry material into the injection molding machine for injection molding. The injection molding temperature is 230°C. During the injection molding process, a special screw is used for stirring.
Embodiment 2
[0030] A formula for making marble texture, in percentage terms, including: polylaurolactam 96%, toner 0.05%, color masterbatch 3.95%, wherein, color masterbatch includes: polylaurolactam 65%, titanium dioxide 32% and pigment 3%.
[0031] The production process of the marble texture includes:
[0032] Step 1, mixing and grinding the above-mentioned polylaurolactam, titanium dioxide and pigment to form a masterbatch;
[0033] Step 2, stirring and mixing the polylaurolactam, toner, and color masterbatch in the amount of the above formula;
[0034] Step 3, putting the mixture into a dehumidifier for drying; the drying temperature of the dehumidifier is 100°C. The drying time is 7 hours.
[0035] Step 4, put the dry material into the injection molding machine for injection molding. The injection molding temperature is 230°C. During the injection molding process, a special screw is used for stirring.
Embodiment 3
[0037] A formula for making marble texture, in percentage terms, including: polylaurolactam 95.96%, toner 0.06%, color masterbatch 4%, wherein, color masterbatch includes: polylaurolactam 63%, titanium dioxide 35% and pigment 2%.
[0038] The production process of the marble texture includes:
[0039] Step 1, mixing and grinding the above-mentioned polylaurolactam, titanium dioxide and pigment to form a masterbatch;
[0040] Step 2, stirring and mixing the polylaurolactam, toner, and color masterbatch in the amount of the above formula;
[0041] Step 3, putting the mixture into a dehumidifier for drying; the drying temperature of the dehumidifier is 100°C. The drying time is 8 hours.
[0042] Step 4, put the dry material into the injection molding machine for injection molding. The injection molding temperature is 240°C. During the injection molding process, a special screw is used for stirring.
PUM
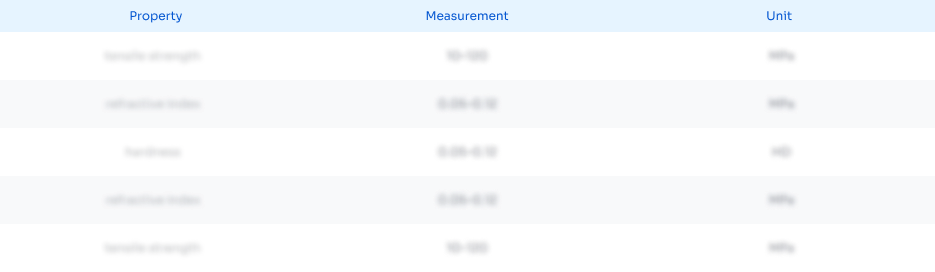
Abstract
Description
Claims
Application Information

- R&D Engineer
- R&D Manager
- IP Professional
- Industry Leading Data Capabilities
- Powerful AI technology
- Patent DNA Extraction
Browse by: Latest US Patents, China's latest patents, Technical Efficacy Thesaurus, Application Domain, Technology Topic, Popular Technical Reports.
© 2024 PatSnap. All rights reserved.Legal|Privacy policy|Modern Slavery Act Transparency Statement|Sitemap|About US| Contact US: help@patsnap.com