Cryolite production process without discharge of waste water
A production process, cryolite technology, applied in the direction of aluminum fluoride, aluminum halide, ammonium chloride, etc., to achieve the effect of saving consumption, less volatilization loss, and stable electrolysis
- Summary
- Abstract
- Description
- Claims
- Application Information
AI Technical Summary
Problems solved by technology
Method used
Examples
Embodiment 1
[0019] 1. Pulping: Put 1.5t of alumina slag and water into the pulping tank and stir to make slurry;
[0020] 2. Reaction: Send the slurry prepared in step 1 to the reaction tank, pass steam into the reaction tank and heat to 80°C, add concentrated sulfuric acid and brine to keep the pH value of the reaction environment at 2.5, and stir the reaction to the end;
[0021] 3. Centrifugal separation: After the reaction, the material is subjected to centrifugal separation, and the crude cryolite and filtrate are separated.
[0022] 4. The crude cryolite separated in step 3 is eluted with water to obtain a wet cryolite product with a water content of about 10%; the wet cryolite product is finally dried with hot air to obtain a cryolite product; the eluted water is combined with the filtrate of step 3 ;
[0023] 5. Precipitation: send the filtrate of step 3 and the eluting water of step 4 into the sedimentation tank together for precipitation, and the recovered water contains a smal...
Embodiment 2
[0027] 1. Pulping: Put 1.5t of alumina slag and water into the pulping tank and stir to make slurry;
[0028] 2. Reaction: Send the slurry prepared in step 1 to the reaction tank, pass steam into the reaction tank and heat to 80°C, add concentrated sulfuric acid and brine to keep the pH value of the reaction environment at 3, and stir the reaction to the end;
[0029] 3. Centrifugal separation: After the reaction, the material is subjected to centrifugal separation, and the crude cryolite and filtrate are separated.
[0030] 4. The crude cryolite separated in step 3 is eluted with water to obtain a wet cryolite product with a water content of about 10%; the wet cryolite product is finally dried with hot air to obtain a cryolite product; the eluted water is combined with the filtrate of step 3 ;
[0031] 5. Precipitation: send the filtrate of step 3 and the eluting water of step 4 into the sedimentation tank together for precipitation, and the recovered water contains a small ...
PUM
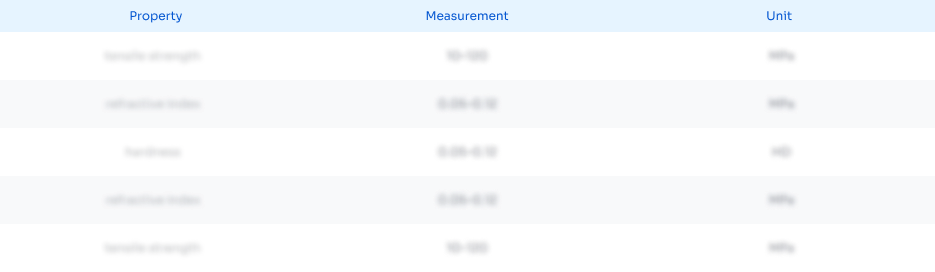
Abstract
Description
Claims
Application Information

- Generate Ideas
- Intellectual Property
- Life Sciences
- Materials
- Tech Scout
- Unparalleled Data Quality
- Higher Quality Content
- 60% Fewer Hallucinations
Browse by: Latest US Patents, China's latest patents, Technical Efficacy Thesaurus, Application Domain, Technology Topic, Popular Technical Reports.
© 2025 PatSnap. All rights reserved.Legal|Privacy policy|Modern Slavery Act Transparency Statement|Sitemap|About US| Contact US: help@patsnap.com