Method for co-bonding embedded copper strip and composite prepreg
A technology of composite materials and prepregs, which is applied in the processing field of glass fiber reinforced resin matrix composite materials, can solve the problems of difficult positioning and fixing, the shape of parts cannot be shaped, and difficult fixing, so as to avoid positioning deviation, solve the difficulty of shaping, and avoid offset effect
- Summary
- Abstract
- Description
- Claims
- Application Information
AI Technical Summary
Problems solved by technology
Method used
Image
Examples
Embodiment 1
[0036] Such as figure 1 As shown, a co-bonding method of embedded copper tape and composite material prepreg is used for co-bonding of embedded copper tape and glass fiber reinforced resin matrix composite material in the vacuum bag-autoclave molding process. During the material laying process, the metal copper tape is bonded to the laid and cured prepreg with an adhesive material, and then the laying and curing of the prepreg is continued in two steps to make it solidified and formed.
[0037] The co-gluing method specifically comprises the following steps:
[0038] S1: Lay the glass fiber reinforced resin-based composite material prepreg on the part tooling mold to the layer before the metal copper strip is placed, and after packaging and compacting in a vacuum bag, perform the first pre-curing in an autoclave. The prepreg is cured to obtain a first precured blank.
[0039] S3: bonding the metal copper strip with an adhesive material, and then placing the metal copper stri...
Embodiment 2
[0043] This embodiment is improved on the basis of Example 1, and the improvement is that: the embedded copper strip blank obtained in S3 is also provided with step S4, and the S4 is to heat and solidify the embedded copper strip blank, which adds The curing temperature of warm curing exceeds the gel point of the bonding material, so that the copper strip and the first-cured blank are fully bonded and fixed on the first-cured blank, avoiding the deviation of the metal copper strip when the prepreg is continued to be laid , Solved the problem of difficult shaping of the metal copper strip due to its thinness.
[0044] The co-gluing method specifically comprises the following steps:
[0045]S1: Lay the glass fiber reinforced resin-based composite material prepreg on the part tooling mold to the layer before the metal copper strip is placed, and after packaging and compacting in a vacuum bag, perform the first pre-curing in an autoclave. The prepreg is cured to obtain a first pr...
Embodiment 3
[0052] This embodiment is improved on the basis of Embodiment 2. The improvement is that in the above S7, after the remaining prepregs are laid up, an equalizing film is placed on the prepregs, and then sealed with a vacuum bag. Send it into an autoclave for curing to make the outer surface of the product smooth and ensure the quality of the non-film surface. Preferably, the pressure equalizing membrane is prepared by curing vulcanized rubber.
[0053] The co-gluing method specifically comprises the following steps:
[0054] S1: Lay the glass fiber reinforced resin-based composite material prepreg on the part tooling mold to the layer before the metal copper strip is placed, and after packaging and compacting in a vacuum bag, perform the first pre-curing in an autoclave. The prepreg is cured to obtain a first precured blank.
[0055] S3: Bond the metal copper strip with an adhesive material, then place the metal copper strip on the surface of the first pre-cured blank, and g...
PUM
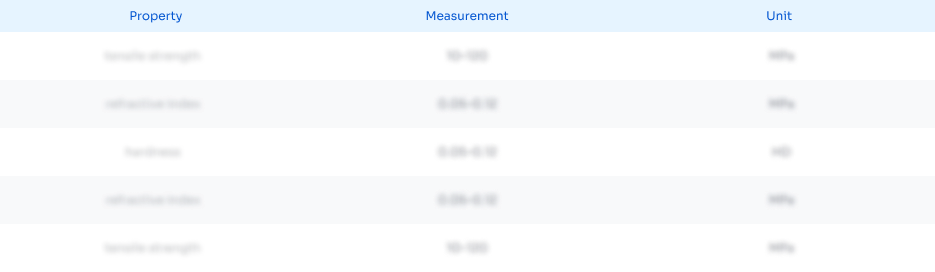
Abstract
Description
Claims
Application Information

- R&D
- Intellectual Property
- Life Sciences
- Materials
- Tech Scout
- Unparalleled Data Quality
- Higher Quality Content
- 60% Fewer Hallucinations
Browse by: Latest US Patents, China's latest patents, Technical Efficacy Thesaurus, Application Domain, Technology Topic, Popular Technical Reports.
© 2025 PatSnap. All rights reserved.Legal|Privacy policy|Modern Slavery Act Transparency Statement|Sitemap|About US| Contact US: help@patsnap.com