A laser cavitation surface pretreatment device and method
A surface pretreatment and cavitation technology, which is applied in laser welding equipment, metal processing equipment, welding equipment, etc., can solve problems such as ablation of carbon fiber materials, carbon fiber material cracks, fractures, etc., to improve surface bonding strength, easy to glue connection, high surface quality
- Summary
- Abstract
- Description
- Claims
- Application Information
AI Technical Summary
Problems solved by technology
Method used
Image
Examples
Embodiment 1
[0043] Select the material 6 to be treated as T300 / epoxy resin composite material, the surface is impurities to be treated and epoxy resin, place the material 6 to be treated in the container 5 and add liquid medium 9 as water, so that the upper surface of the material is at a height distance from the water surface h=5mm; the container 5 is placed on the mobile platform 7, and the movement of the mobile platform 7 is controlled by the control system 1, so that the distance between the impurities 8 on the upper surface of the material and the focal plane of the focusing lens 4 is h 0 =1 mm; the direction of the laser beam is adjusted by the scanning galvanometer 3 so that it is parallel to the normal direction of the upper surface of the material 6 to be processed.
[0044] Set laser energy, J 0 +J 1 +J 2 ≤J≤J 0 +J 2 +J 3 . Among them, J 0 =J w (1+αh),α=14.6171m -1 , J w =0.4mJ,J 0 =0.6mJ;J 1 = 15mJ; J 2 =5mJ;J 3 = 60mJ. That is, 21mJ≤J≤66mJ. Set the laser energ...
Embodiment 2
[0047] Select material 6 to be treated as T300 / epoxy resin composite material, the surface is impurity to be processed and epoxy resin, material 6 to be treated is placed in container 5 and then adding liquid medium 9 is 10% glycerin aqueous solution, so that the distance between the upper surface of the material The liquid surface height distance h=5mm; the movement of the mobile platform 7 is controlled by the control system 1, so that the distance between the impurities 8 on the upper surface of the material and the focal plane of the focusing lens 4 is increased to h 0 =2mm; the direction of the laser beam is adjusted by the scanning galvanometer 3 so that it is parallel to the normal direction of the upper surface of the material 6 to be processed. The laser energy was increased to J=50mJ.
[0048] Such as image 3 Shown as J=50mJ, h=5mm, h 0 =2mm SEM images of laser cavitation surface pretreatment of carbon fiber composite materials. It is found from the images that th...
Embodiment 3
[0050] All preparations are the same as in Example 1, and the distance between the upper surface of the material and the height of the water surface is increased to be h=10mm; the impurity 8 on the upper surface of the material and the focal plane distance of the focusing lens 4 are h 0 =2mm; laser energy J=50mJ.
[0051] Such as Figure 4 Shown as J=50mJ, h=10mm, h 0 =2mm SEM image of carbon fiber composite material laser cavitation surface pretreatment, it is found from the image that the surface removal effect is better, the carbon fiber matrix is complete, and there is no fracture. Compared with Example 1, the energy loss increases, the removal area expands, the surface has almost no undulations, and the modification effect is poor.
PUM
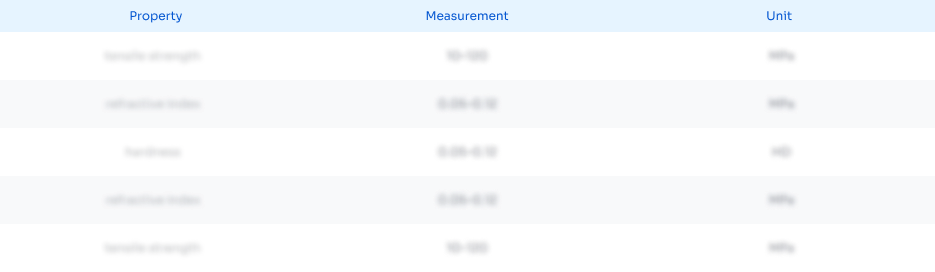
Abstract
Description
Claims
Application Information

- Generate Ideas
- Intellectual Property
- Life Sciences
- Materials
- Tech Scout
- Unparalleled Data Quality
- Higher Quality Content
- 60% Fewer Hallucinations
Browse by: Latest US Patents, China's latest patents, Technical Efficacy Thesaurus, Application Domain, Technology Topic, Popular Technical Reports.
© 2025 PatSnap. All rights reserved.Legal|Privacy policy|Modern Slavery Act Transparency Statement|Sitemap|About US| Contact US: help@patsnap.com