Automatic demolding and trimming PP plastic part forming equipment and process
A technology for automatic demoulding and molding equipment, which is applied to household components, household appliances, and other household appliances. It can solve the problems of easy damage to the surface of the table, labor-intensive, manual operation, etc., to achieve clean and thorough cutting, and improve effect of effect
- Summary
- Abstract
- Description
- Claims
- Application Information
AI Technical Summary
Problems solved by technology
Method used
Image
Examples
Embodiment 1
[0051] Such as figure 1 , figure 2 , image 3 , Figure 4 , Figure 5 , Figure 6 , Figure 7 , Figure 8 , Figure 9 , Figure 10 , Figure 11 , Figure 12 As shown, a PP plastic part molding equipment for automatic demoulding and trimming includes a molding device 1, and the molding device 1 includes a punch mechanism 11, a concave mold mechanism 12 that is formed in cooperation with the punch mechanism 11, and is arranged on a convex mold mechanism. The injection mechanism 13 above between the die mechanism 11 and the die mechanism 12; also includes the discharge device 2 arranged on one side of the injection mechanism 13 and the trimming device arranged on the same side of the punch mechanism 11 and the die mechanism 12 3;
[0052] The discharge device 2 includes a fixing mechanism 21 for absorbing and fixing the side waste 101 of the table 10 that has been formed and left on the die mechanism 12, and for driving the fixing mechanism 21 and the table 10 absorbe...
Embodiment 2
[0069] Such as figure 1 , figure 2 , image 3 , Figure 4 , Figure 5 , Figure 6 , Figure 7 , Figure 8 , Figure 9 , Figure 10 , Figure 11 , Figure 12As shown, the components that are the same as or corresponding to those in the first embodiment are marked with the corresponding reference numerals in the first embodiment. For the sake of simplicity, only the differences from the first embodiment will be described below. The difference between the second embodiment and the first embodiment is that the turning mechanism 22 includes a driving member 221 fixed on the die frame 121 and a third gear 222 fixed on the rotating shaft 2115 and arranged coaxially with the rotating shaft 2115, The end of the driving member 221 is provided with a rack portion 223 that cooperates with the third gear 222 , and the rack portion 223 drives the third gear 222 together with the adsorption plate 2112 to rotate 90° during the opening process of the die frame 121 .
[0070] In thi...
Embodiment 3
[0072] Such as Figure 13 As shown, a PP plastic part molding process with automatic demoulding and trimming includes the following production steps:
[0073] a. Forming process, the injection mechanism 13 extrudes the raw material to the forming station, and the punch mechanism 11 and the die mechanism 12 cooperate to extrude the raw material at the forming station;
[0074] b. demoulding process, the punch mechanism 11 and the die mechanism 12 are opened to a certain position, and the fixing mechanism 21 utilizes the negative pressure adsorption force to absorb and fix the edge waste 101 of the table 10 left on the die mechanism 12, The punch mechanism 11 and the die mechanism 12 continue to open the mold, and the table plate 10 breaks away from the die mechanism 12;
[0075] c. Overturning process, during the mold opening process of the punch mechanism 11 and the concave mold mechanism 12, the overturn mechanism 22 drives the two adsorption components of the fixing mechani...
PUM
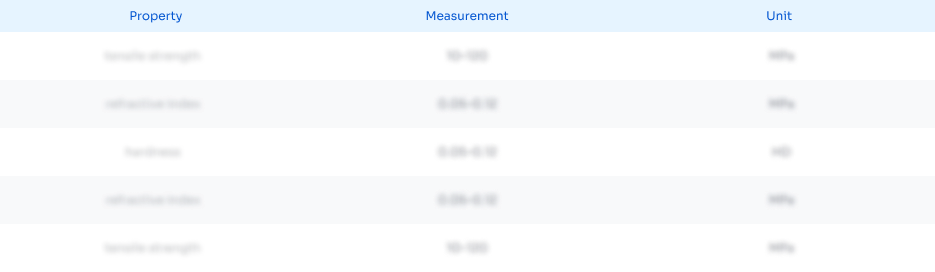
Abstract
Description
Claims
Application Information

- R&D
- Intellectual Property
- Life Sciences
- Materials
- Tech Scout
- Unparalleled Data Quality
- Higher Quality Content
- 60% Fewer Hallucinations
Browse by: Latest US Patents, China's latest patents, Technical Efficacy Thesaurus, Application Domain, Technology Topic, Popular Technical Reports.
© 2025 PatSnap. All rights reserved.Legal|Privacy policy|Modern Slavery Act Transparency Statement|Sitemap|About US| Contact US: help@patsnap.com