Preparation method of composite filtering element and composite filtering element
A technology of composite filter elements and filter elements, which is applied in the direction of filtration separation, separation methods, chemical instruments and methods, etc., can solve problems such as uneven enhancement effect, decrease in uniformity of filter element strength, and damage to filter elements, so as to overcome brittleness Rapid increase, increased strength, isotropic uniform effect
- Summary
- Abstract
- Description
- Claims
- Application Information
AI Technical Summary
Problems solved by technology
Method used
Image
Examples
Embodiment 1
[0029] A preparation method of a composite filter element, comprising the steps of:
[0030] a: prepare the first filter element 1 and the second filter element 4 with a filter surface 2 and a plane 3 respectively of the same size, and the first filter element 1 and the second filter element 4 are obtained by gathering molten raw materials respectively Acrylic is pressed in half filter element molds.
[0031] B: prepare reinforcing material layer 5: carbon fiber is made into the reinforcing material layer 5 of the mesh structure matching with the size of the first filter element 1 and the second filter element 4 by weaving, and the mesh structure is set as a plain weave mesh structure.
[0032] c: The reinforcing material layer 5 prepared in step b is fixed between the planes of the first filter element 1 prepared in step a and the plane of the second filter element 4 by means of plane hot-melt, that is, the preparation of the composite filter element is completed.
[0033] ...
Embodiment 2
[0035] A preparation method of a composite filter element, comprising the steps of:
[0036] a: prepare the first filter element and the second filter element with a filter surface and a plane respectively of the same size, and the first filter element and the second filter element are respectively passed through the raw material polyethylene of melting in half filter element Pressed in a mould.
[0037] b: Preparing the reinforcing material layer: the carbon fiber is made into a reinforcing material layer of a mesh structure matching the size of the first filter element and the second filter element by weaving, and the mesh structure is set as a twill mesh structure.
[0038] c: The reinforcing material layer prepared in step b is fixed between the planes of the first filter element prepared in step a and the plane of the second filter element by plane welding, that is, the preparation of the composite filter element is completed.
Embodiment 3
[0040] A preparation method of a composite filter element, comprising the steps of:
[0041] a: prepare the first filter element and the second filter element with a filter surface and a plane respectively of the same size, the first filter element and the second filter element are respectively passed through the raw material polypropylene of melting in half filter element Pressed in a mould.
[0042] b: Preparation of reinforcement material layer: the glass fiber is made into a random reinforcement mat or reinforcement mat or non-woven fabric matching the size of the first filter element and the second filter element through a non-woven method.
[0043] c: The reinforcing material layer prepared in step b is fixed between the planes of the first filter element prepared in step a and the plane of the second filter element by plane cold bonding, that is, the preparation of the composite filter element is completed.
PUM
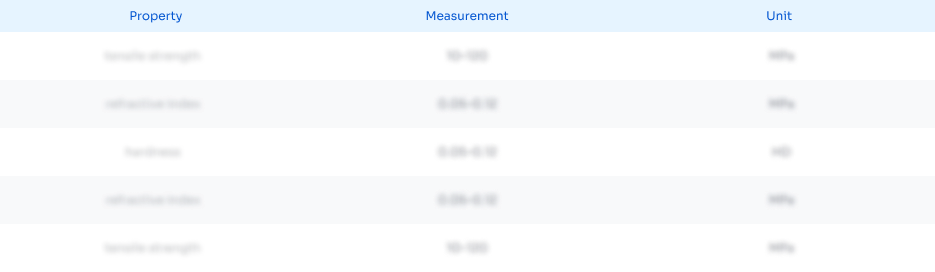
Abstract
Description
Claims
Application Information

- R&D
- Intellectual Property
- Life Sciences
- Materials
- Tech Scout
- Unparalleled Data Quality
- Higher Quality Content
- 60% Fewer Hallucinations
Browse by: Latest US Patents, China's latest patents, Technical Efficacy Thesaurus, Application Domain, Technology Topic, Popular Technical Reports.
© 2025 PatSnap. All rights reserved.Legal|Privacy policy|Modern Slavery Act Transparency Statement|Sitemap|About US| Contact US: help@patsnap.com