A flame-retardant heat-conducting recycled PS composite material and its preparation method
A composite material and flame retardant technology, which is applied in the field of flame retardant and thermally conductive recycled PS composite materials and their preparation, can solve the problems of poor flame retardancy, low toughness of recycled PS materials, and general thermal conductivity, and achieves excellent thermal conductivity and large promotion. Meaningful, low-cost effects
- Summary
- Abstract
- Description
- Claims
- Application Information
AI Technical Summary
Problems solved by technology
Method used
Image
Examples
preparation example Construction
[0032] The preparation method of any one of the above flame-retardant and heat-conducting recycled PS composite materials comprises the following steps:
[0033] (1) Weigh 80-100 parts of recycled PS, 20-30 parts of recycled PC, 12-16 parts of flame retardant, 3-5 parts of calcium silicate whiskers, 8-12 parts of Bi 2 o 3 , 0.1-0.5 parts of antioxidant, 0.1-0.3 parts of SEBS-g-MAH are mixed and stirred evenly to obtain a mixture;
[0034] (2) Extruding and granulating the mixture obtained in step (1) through a twin-screw extruder to obtain a PS composite material.
[0035] The step (2) is specifically: put the mixture obtained in the step (1) into the hopper of the twin-screw extruder and extrude and granulate to obtain the PS composite material, wherein the twin-screw extruder includes sequentially arranged There are six temperature zones, the first zone temperature is 160-180°C, the second zone temperature is 210-250°C, the third zone temperature is 210-250°C, the fourth z...
Embodiment 1
[0037] (1) Weigh 80 parts of recovered PS, 20 parts of recovered PC, 9 parts of octabromobisphenol S ether, 3 parts of anhydrous magnesium carbonate, 3 parts of calcium silicate whiskers, and 8 parts of Bi 2 o 3 , 0.1 part of Irganox168, and 0.1 part of SEBS-g-MAH were mixed and stirred evenly to obtain a mixture;
[0038] (2) Extruding and granulating the mixture obtained in the step (1) to obtain the recycled PS composite material P1.
[0039] Among them, the temperature and screw speed of each zone of the twin-screw extruder are respectively: the temperature of the first zone is 160°C, the temperature of the second zone is 210°C, the temperature of the third zone is 210°C, the temperature of the fourth zone is 210°C, the temperature of the fifth zone is 210°C, the temperature of the sixth zone is 210°C, The head temperature is 210°C, and the screw speed is 200r / min.
Embodiment 2
[0041] (1) Weigh 100 parts of recovered PS, 30 parts of recovered PC, 12 parts of octabromobisphenol S ether, 4 parts of anhydrous magnesium carbonate, 5 parts of calcium silicate whiskers, 12 parts of Bi 2 o 3 , 0.1 part of Irganox168, 0.2 part of Irganox1010, 0.2 part of Irganox1330, 0.3 part of SEBS-g-MAH were mixed and stirred evenly to obtain a mixture;
[0042] (2) Extruding and granulating the mixture obtained in the step (1) to obtain the recycled PS composite material P2.
[0043] Among them, the temperature and screw speed of each zone of the twin-screw extruder are respectively: the temperature of the first zone is 180°C, the temperature of the second zone is 250°C, the temperature of the third zone is 250°C, the temperature of the fourth zone is 250°C, the temperature of the fifth zone is 250°C, and the temperature of the sixth zone is 250°C. The head temperature is 250°C, and the screw speed is 280r / min.
PUM
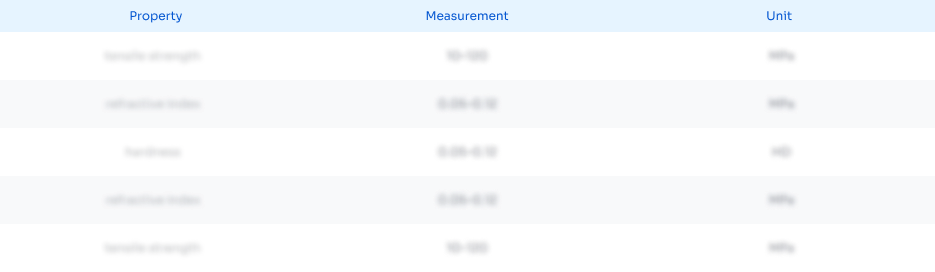
Abstract
Description
Claims
Application Information

- R&D
- Intellectual Property
- Life Sciences
- Materials
- Tech Scout
- Unparalleled Data Quality
- Higher Quality Content
- 60% Fewer Hallucinations
Browse by: Latest US Patents, China's latest patents, Technical Efficacy Thesaurus, Application Domain, Technology Topic, Popular Technical Reports.
© 2025 PatSnap. All rights reserved.Legal|Privacy policy|Modern Slavery Act Transparency Statement|Sitemap|About US| Contact US: help@patsnap.com