Stretching and pressing combined type plate stretch forming machine
A stretch forming and composite technology, applied to aircraft parts, feeding devices, positioning devices, etc., can solve the problems of expensive equipment, large transition area allowance, high manufacturing cost, etc., and achieve the simplification of hydraulic control system and electrical control system , uniform distribution of tensile stress and strain, and the effect of reducing the margin of the transition zone
- Summary
- Abstract
- Description
- Claims
- Application Information
AI Technical Summary
Problems solved by technology
Method used
Image
Examples
Embodiment Construction
[0022] The specific content and working process of the present invention will be further described below in conjunction with the embodiments shown in the drawings.
[0023] The pressing device of the tension-compression composite sheet metal stretching forming machine of the present invention is composed of a plurality of pressing mechanisms arranged in a row, and the pressing mechanism is composed of rollers, hydraulic cylinders, pins and brackets. In the process of drawing and forming of the sheet, due to the uneven deformation and double curvature deformation of each part of the sheet, the roller can produce a certain corner with the pin as the center to adapt to the change of the sheet. The clamping mechanism of the stretch forming machine is composed of clamps, hinged rods, return springs and guide rollers. The clamps are composed of hydraulic cylinders, clamping racks, upper and lower clamping blocks, and are arranged in a row with the hinged rods. Head swing function. The...
PUM
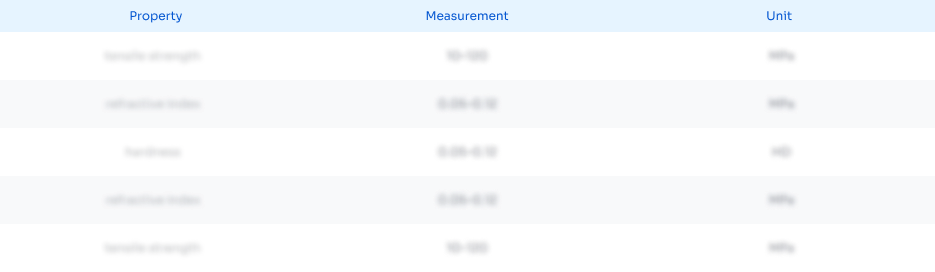
Abstract
Description
Claims
Application Information

- R&D
- Intellectual Property
- Life Sciences
- Materials
- Tech Scout
- Unparalleled Data Quality
- Higher Quality Content
- 60% Fewer Hallucinations
Browse by: Latest US Patents, China's latest patents, Technical Efficacy Thesaurus, Application Domain, Technology Topic, Popular Technical Reports.
© 2025 PatSnap. All rights reserved.Legal|Privacy policy|Modern Slavery Act Transparency Statement|Sitemap|About US| Contact US: help@patsnap.com