Thread cutting device for sewing machine
A sewing machine and thread cutting technology, which is applied to the thread cutting mechanism, sewing machine components, sewing equipment and other directions in the sewing machine, can solve the problems of complex structure, affecting product appearance and sewing quality, and low production efficiency.
- Summary
- Abstract
- Description
- Claims
- Application Information
AI Technical Summary
Problems solved by technology
Method used
Image
Examples
Embodiment 1
[0043] Such as figure 2 , image 3 , Image 6 with Figure 7 As shown, the electric heat cutting assembly 1 includes a push plate 10, an electric heat cutter 11 and an electric heater for heating the electric heat cutter 11, the push plate 10 also includes a connecting arm 101, the connecting arm 101 and the driving arm 102 are arranged in parallel, and the thread cutting arm 103 is connected to one side edge of connecting arm 101, and is set toward the extension direction of connecting arm 101, because the size of needle plate 4 is smaller, setting tangent arm 103 is longer than driving arm 102—in order to carry out structure during the movement process of pushing plate 10 Dodging is also convenient for the power cord of the electric heater to be arranged. The second is to simplify the structure; the electric thermal cutter 11 is located at the bottom of the thread cutting arm 103, and the wire hook groove 1031 is arranged at the front end of the thread cutting arm 103. Th...
Embodiment 2
[0049] The difference between this embodiment and Embodiment 1 is that, as Figure 4 , Image 6 with Figure 7 As shown, the driving device 2 includes an electromagnet 204, a pull rod 205 and a transmission rod 206, the pull rod 205 is connected to the electromagnet 204, and a spring 2051 is sleeved on the pull rod 205, and the two ends of the spring 2051 abut against the electromagnet 204 and the transmission rod respectively 206, one end of the transmission rod 206 is connected to the pull rod 205, and the other end is connected to the driving arm 102. Specifically, when the thread is cut, the electromagnet 204 is energized, and the electromagnet 204 generates magnetism after being energized, and the pull rod 205 is close to the electromagnet 204 under the action of magnetic force. movement, the spring 2051 is compressed, driving the transmission rod 206 to move towards the direction close to the electromagnet 204, and then driving the push plate 10 to move, so that the thr...
Embodiment 3
[0051] The difference between this embodiment and Embodiment 1 is that, as Figure 5 , Image 6 with Figure 7 As shown, the electric heating thread cutting assembly 1 is entirely arranged on the needle plate 4, which is beneficial to simplify the overall structure of the sewing machine. The needle plate 4 is provided with a chute 31 for the sliding of the push plate 10, and the two ends of the limit plate 105 pass through the limit column 106. It is fixed in the chute 31. Specifically, the needle plate 4 includes a notch part and a mounting part. The notch part has an arc surface matching the concave arc surface of the feeding dog 6, and the feeding dog notch 42 is arranged on the needle. The notch of the plate 4 matches the teeth 63 of the feed dog 6, the pinhole 41 is set on the notch of the needle plate 4, and the installation part is arranged flat. The thread cutting arm 103 on the plate 10 is driven by the driving device 2 to move towards the needle hole 41 in the notc...
PUM
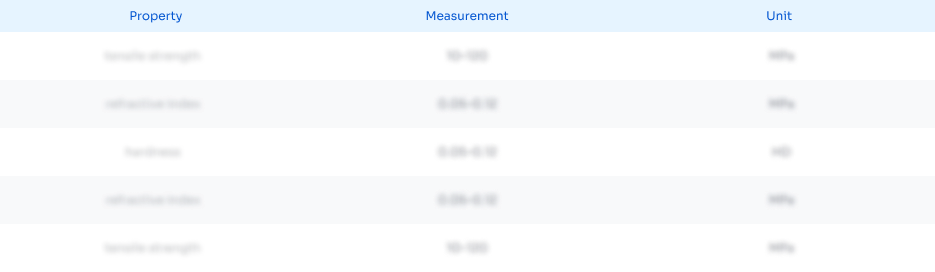
Abstract
Description
Claims
Application Information

- Generate Ideas
- Intellectual Property
- Life Sciences
- Materials
- Tech Scout
- Unparalleled Data Quality
- Higher Quality Content
- 60% Fewer Hallucinations
Browse by: Latest US Patents, China's latest patents, Technical Efficacy Thesaurus, Application Domain, Technology Topic, Popular Technical Reports.
© 2025 PatSnap. All rights reserved.Legal|Privacy policy|Modern Slavery Act Transparency Statement|Sitemap|About US| Contact US: help@patsnap.com