A punching process for sheet metal round holes
A process and plate technology, applied in the field of plate round hole punching process, can solve problems such as major safety, hidden dangers, equipment clamping, etc., and achieve the effect of accurate processing
- Summary
- Abstract
- Description
- Claims
- Application Information
AI Technical Summary
Problems solved by technology
Method used
Image
Examples
Embodiment Construction
[0033] In order to make the technical means, creative features, goals and effects achieved by the present invention easy to understand, the present invention will be further described below in conjunction with specific embodiments.
[0034] Such as Figure 1-Figure 7 As shown in the present invention, a plate hole stamping process is characterized in that: the process comprises the following steps:
[0035] S1, cutting the material from the large plate with a cutting machine;
[0036] S2, putting the material cut in S1 into a heat treatment box for heating; after a period of time, cooling the material at room temperature;
[0037] S3, putting the cooled material in S2 into a hydraulic press for punching;
[0038] S4, put the punched material of S3 into the heat treatment equipment for heating, after a period of time, put the material into cold water for quenching;
[0039] After S5 and S4 are completed, put the material in S4 into the hydraulic press and replace the punching ...
PUM
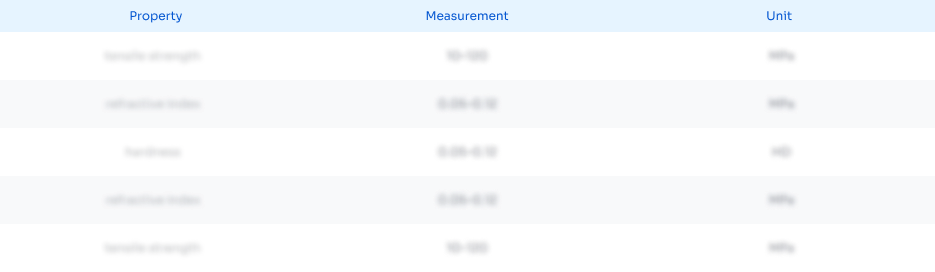
Abstract
Description
Claims
Application Information

- R&D Engineer
- R&D Manager
- IP Professional
- Industry Leading Data Capabilities
- Powerful AI technology
- Patent DNA Extraction
Browse by: Latest US Patents, China's latest patents, Technical Efficacy Thesaurus, Application Domain, Technology Topic, Popular Technical Reports.
© 2024 PatSnap. All rights reserved.Legal|Privacy policy|Modern Slavery Act Transparency Statement|Sitemap|About US| Contact US: help@patsnap.com