Sweater-resistant foam extinguishing agent
A foam fire extinguishing agent and seawater-resistant technology, applied in fire prevention equipment, etc., can solve the problems of high production cost, poor foaming effect, complex composition, etc., and achieve the effect of improving product properties, avoiding excessive corrosion, and increasing viscosity
- Summary
- Abstract
- Description
- Claims
- Application Information
AI Technical Summary
Problems solved by technology
Method used
Image
Examples
Embodiment 1
[0020] (1) 15 parts by mass of sulfobetaine, 10 parts of cocamidopropyl betaine, and 25 parts of water were reacted at 45° C. to prepare a betaine surfactant.
[0021] (2) The hydrolyzed protein suspension obtained after high-speed stirring of 12 parts by mass of hydrolyzed soybean protein, 12 parts of hydrolyzed keratin, 3 parts of hydrolyzed porcine blood protein, 2 parts of urea, and 25 parts of water.
[0022] (3) Add 15 parts of aluminum trichloride, 3 parts of ferric chloride, and 4 parts of calcium chloride into a stirrer and mix uniformly to obtain chloride.
[0023] (4) The stabilizer obtained after uniformly mixing 15 parts by mass of ethylene glycol and 6 parts of glycerol.
[0024] (5) Add 50 parts of water in the reactor, control the temperature of the reactor at 45°C, then add 12 parts of betaine surfactant and carry out constant temperature reaction for 2 hours, add 10 parts of Hydrolyzed protein, 6 parts of chloride, 7 parts of urea, 8 parts of higher alcohol,...
Embodiment 2
[0026] (1) 12 parts by mass of sulfobetaine, 8 parts of cocamidopropyl betaine, and 20 parts of water were reacted at 45°C to prepare a betaine surfactant.
[0027] (2) The hydrolyzed protein suspension obtained after high-speed stirring of 12 parts by mass of hydrolyzed soybean protein, 14 parts of hydrolyzed keratin, 4 parts of hydrolyzed porcine blood protein, 1 part of urea, and 25 parts of water.
[0028] (3) Add 12 parts of aluminum trichloride, 4 parts of ferric chloride, and 4 parts of calcium chloride into a stirrer for uniform mixing to obtain chloride.
[0029] (4) The stabilizer obtained after uniformly mixing 12 parts by mass of ethylene glycol and 6 parts of glycerol.
[0030] (5) Add 60 parts of water in the reactor, control the temperature of the reactor at 50°C, then add 12 parts of betaine surfactant and carry out constant temperature reaction for 2 hours, add 9 parts of Hydrolyzed protein, 6 parts of chloride, 8 parts of urea, 9 parts of higher alcohol, 4 p...
Embodiment 3
[0032] (1) 16 parts by mass of sulfobetaine, 8 parts of cocamidopropyl betaine, and 30 parts of water were reacted at 40-50° C. to obtain a betaine surfactant.
[0033] (2) The hydrolyzed protein suspension obtained after high-speed stirring of 10 parts by mass of hydrolyzed soybean protein, 15 parts of hydrolyzed keratin, 2 parts of hydrolyzed porcine blood protein, 2 parts of urea, and 30 parts of water.
[0034] (3) Add 12 parts of aluminum trichloride, 2 parts of ferric chloride, and 3 parts of calcium chloride into a stirrer and mix uniformly to obtain chloride.
[0035] (4) A stabilizer obtained by uniformly mixing 16 parts by mass of ethylene glycol and 6 parts of glycerol.
[0036] (5) Add 60 parts of water in the reactor, control the temperature of the reactor at 60°C, then add 11 parts of betaine surfactant and carry out constant temperature reaction for 2 hours, add 10 parts of Hydrolyzed protein, 5 parts of chloride, 8 parts of urea, 7 parts of higher alcohol, 4 p...
PUM
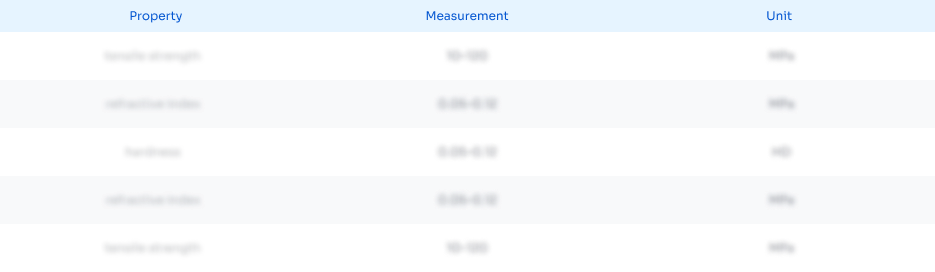
Abstract
Description
Claims
Application Information

- R&D Engineer
- R&D Manager
- IP Professional
- Industry Leading Data Capabilities
- Powerful AI technology
- Patent DNA Extraction
Browse by: Latest US Patents, China's latest patents, Technical Efficacy Thesaurus, Application Domain, Technology Topic, Popular Technical Reports.
© 2024 PatSnap. All rights reserved.Legal|Privacy policy|Modern Slavery Act Transparency Statement|Sitemap|About US| Contact US: help@patsnap.com