Coupling joint for plane joint robot and manufacturing equipment for coupling joint
A technology of planar joints and manufacturing equipment, which is applied in the field of robotics, can solve problems such as poor heavy load bearing capacity, increased manufacturing cost and maintenance cost, unfavorable expansion of the rotation axis, etc., to achieve good self-adaptive adjustment and support capabilities, and to improve The effect of carrying capacity
- Summary
- Abstract
- Description
- Claims
- Application Information
AI Technical Summary
Problems solved by technology
Method used
Image
Examples
Embodiment Construction
[0031] The present invention is described in further detail now in conjunction with accompanying drawing. These drawings are all simplified schematic diagrams, which only illustrate the basic structure of the present invention in a schematic manner, so they only show the configurations related to the present invention.
[0032] Such as figure 1 The shown embodiment of a coupling joint for a planar joint robot of the present invention has a connecting cylinder 1, the upper end of the connecting cylinder 1 is in the shape of a ball head, and the lower end is in the shape of a cylinder, and the lower end of the cylinder can be directly set as a stud The upper end of the connecting cylinder 1 is in the shape of a ball head, and the lubricating sleeve 2 and the connecting housing 3 are arranged in sequence from the inside to the outside. grinding layer, and the lower end of the lubricating sleeve 2 covers the upper end of the connecting cylinder 1, the ball end of the entire conne...
PUM
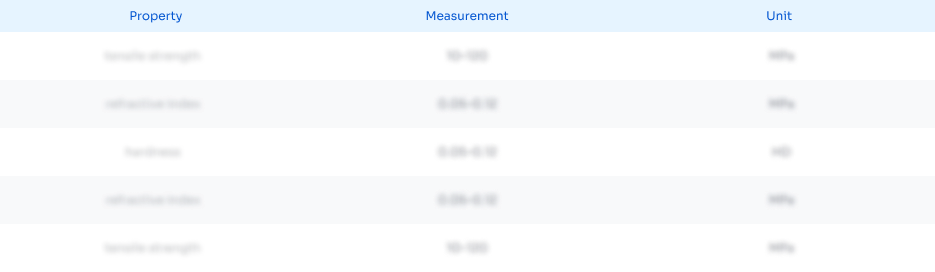
Abstract
Description
Claims
Application Information

- Generate Ideas
- Intellectual Property
- Life Sciences
- Materials
- Tech Scout
- Unparalleled Data Quality
- Higher Quality Content
- 60% Fewer Hallucinations
Browse by: Latest US Patents, China's latest patents, Technical Efficacy Thesaurus, Application Domain, Technology Topic, Popular Technical Reports.
© 2025 PatSnap. All rights reserved.Legal|Privacy policy|Modern Slavery Act Transparency Statement|Sitemap|About US| Contact US: help@patsnap.com