Cathodic electrophoretic coating and preparation method thereof
A cathodic electrophoretic coating and mixing technology, applied in the field of coatings, can solve the problems of general weather resistance, failure to meet the requirements of the field, and high weather resistance requirements, and achieve excellent anti-sedimentation performance, excellent anti-corrosion performance, and good matching effects.
- Summary
- Abstract
- Description
- Claims
- Application Information
AI Technical Summary
Problems solved by technology
Method used
Image
Examples
preparation example Construction
[0030] In one embodiment, the preparation method includes the following steps:
[0031] (1) taking each component according to the raw material ratio of the cathodic electrophoretic coating;
[0032] (2) Mixing and grinding the quaternary ammonium salt dispersion resin, pigments and fillers and deionized water to obtain a color paste;
[0033] (3) Mixing the fluorine-modified epoxy resin, blocked isocyanate, emulsifier, neutralizer and deionized water to obtain an emulsion;
[0034] (4) Mixing the color paste, emulsion and deionized water to obtain cathodic electrophoretic paint.
[0035] The above-mentioned preparation method is further explained below:
[0036] Preferably, in step (4), the stirring speed of the mixing treatment is 1500-2000 rpm, and the stirring is sufficient to obtain a uniform cathodic electrophoretic coating.
[0037] Preferably, in step (2), the grinding fineness of the grinding treatment is ≤15um to ensure the uniformity of the color paste.
[0038]...
Embodiment 1
[0041] A cathodic electrophoretic paint, the raw materials include the following components in mass fractions: 5% of color paste, 45% of emulsion, and 50% of deionized water;
[0042] The color paste includes the following components in parts by mass: 30 parts of quaternary ammonium salt dispersion resin, 50 parts of deionized water, 9 parts of MH-RC, 5 parts of chrome yellow 7000, 6 parts of titanium dioxide;
[0043] The emulsion includes the following components in parts by mass: 30 parts of fluorine-modified epoxy resin, 12 parts of blocked isocyanate, 6 parts of emulsifier, 3 parts of neutralizer, and 50 parts of deionized water.
[0044] The cathodic electrophoretic coating preparation method comprises the following steps:
[0045] (1) take each component according to the described raw material ratio;
[0046] (2) Mixing the quaternary ammonium salt dispersion resin, pigments and fillers, and deionized water for 10-20 minutes, and grinding to a fineness of ≤15um to obta...
Embodiment 2
[0050] A cathodic electrophoretic paint, the raw materials include the following components in mass fractions: 10% of color paste, 40% of emulsion, and 55% of deionized water;
[0051] The color paste includes the following components in parts by mass: 40 parts of quaternary ammonium salt dispersion resin, 45 parts of deionized water, 3 parts of MH-RC, 6 parts of chrome yellow 7000, and 6 parts of titanium dioxide;
[0052] The emulsion includes the following components in parts by mass: 32 parts of fluorine-modified epoxy resin, 9 parts of blocked isocyanate, 2 parts of emulsifier, 7 parts of neutralizer, and 50 parts of deionized water.
[0053] The cathodic electrophoretic coating preparation method comprises the following steps:
[0054] (1) take each component according to the described raw material ratio;
[0055] (2) Mixing the quaternary ammonium salt dispersion resin, pigments and fillers, and deionized water for 10-20 minutes, and grinding to a fineness of ≤15um to ...
PUM
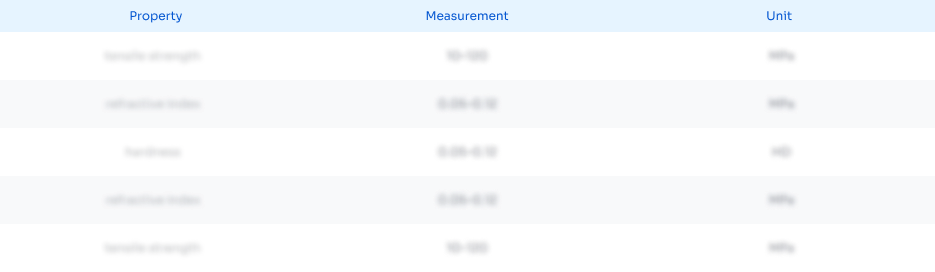
Abstract
Description
Claims
Application Information

- R&D
- Intellectual Property
- Life Sciences
- Materials
- Tech Scout
- Unparalleled Data Quality
- Higher Quality Content
- 60% Fewer Hallucinations
Browse by: Latest US Patents, China's latest patents, Technical Efficacy Thesaurus, Application Domain, Technology Topic, Popular Technical Reports.
© 2025 PatSnap. All rights reserved.Legal|Privacy policy|Modern Slavery Act Transparency Statement|Sitemap|About US| Contact US: help@patsnap.com