Feedback-dissipative Hamiltonian adaptive control system for radial hybrid magnetic bearings
A self-adaptive control, radial hybrid technology, applied in control systems, vector control systems, electronic commutation motor control, etc., can solve the problems of cumbersome implementation steps, large amount of calculation, incomplete factors, etc., and achieve fast and stable system speed. , decoupling control inhibition, the effect of system speed realization
- Summary
- Abstract
- Description
- Claims
- Application Information
AI Technical Summary
Problems solved by technology
Method used
Image
Examples
Embodiment Construction
[0018] In the present invention, the radial hybrid magnetic bearing 6 is used as the controlled object, and the displacement x of the rotor in the radial two degrees of freedom is collected through the X-direction displacement sensor 71 and the Y-direction displacement sensor 73 respectively. *′ and y *′ Signal, X, Y direction radial offset x *′ and y *′ The signals are respectively output through the corresponding X-direction displacement interface circuit 72 and the Y-direction displacement interface circuit 74, respectively corresponding to the rotor radial two-degree-of-freedom reference displacement x * and y * The signals are compared to get the displacement deviation e x and e y Signal. Displacement deviation e x and e y The signal is input to the stable balance point calculation module 1. Considering that the load resistance of the controlled object will have an unstable influence on the rotational speed during operation and hinder the adaptive adjustment of the...
PUM
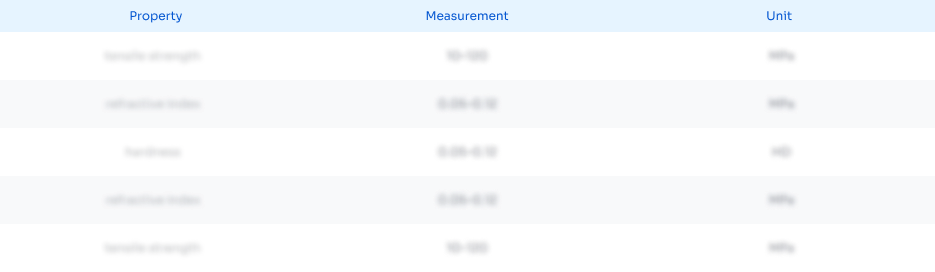
Abstract
Description
Claims
Application Information

- Generate Ideas
- Intellectual Property
- Life Sciences
- Materials
- Tech Scout
- Unparalleled Data Quality
- Higher Quality Content
- 60% Fewer Hallucinations
Browse by: Latest US Patents, China's latest patents, Technical Efficacy Thesaurus, Application Domain, Technology Topic, Popular Technical Reports.
© 2025 PatSnap. All rights reserved.Legal|Privacy policy|Modern Slavery Act Transparency Statement|Sitemap|About US| Contact US: help@patsnap.com