Box-type steel column splice joint and mounting method thereof
An installation method and section steel technology, applied in the direction of building, building structure, etc., can solve the problems of large dislocation of upper and lower sections, reduce on-site welding, and low splicing efficiency of box-shaped steel columns, so as to improve the quality and achieve equal strong connection. Effect
- Summary
- Abstract
- Description
- Claims
- Application Information
AI Technical Summary
Problems solved by technology
Method used
Image
Examples
Embodiment Construction
[0032] In order to facilitate the understanding of the present invention, the present invention will be described in more detail below in conjunction with the accompanying drawings and preferred embodiments, but the protection scope of the present invention is not limited to the following specific embodiments.
[0033] Such as Figure 4 to Figure 6 As shown, the box-shaped steel column splicing node of this embodiment includes an upper column unit 1 and a lower column unit 2, and a connection for connecting the upper column unit 1 and the lower column unit 2 is provided between the upper column unit 1 and the lower column unit 2 Unit 3, one end of the connection unit 3 is fixed to the end inner wall of the lower column unit 2, the other end of the connection unit 3 is higher than the lower column unit 2 and is connected to the end inner wall of the upper column unit 1 after the upper column unit 1 is docked and inserted Fixed. Specifically, the other end of the connection uni...
PUM
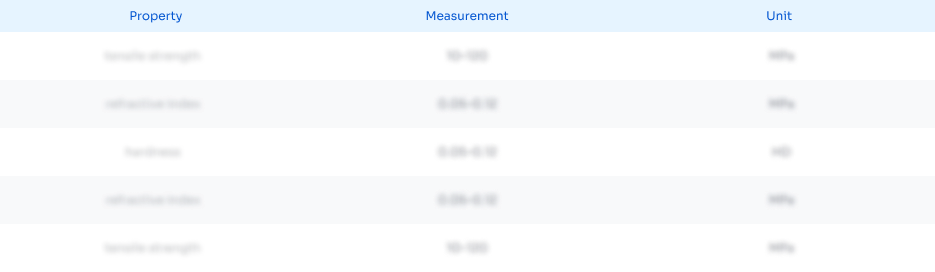
Abstract
Description
Claims
Application Information

- Generate Ideas
- Intellectual Property
- Life Sciences
- Materials
- Tech Scout
- Unparalleled Data Quality
- Higher Quality Content
- 60% Fewer Hallucinations
Browse by: Latest US Patents, China's latest patents, Technical Efficacy Thesaurus, Application Domain, Technology Topic, Popular Technical Reports.
© 2025 PatSnap. All rights reserved.Legal|Privacy policy|Modern Slavery Act Transparency Statement|Sitemap|About US| Contact US: help@patsnap.com