Method for catalytic nitration of o-chlorotoluene by using modified beta zeolite
A technology of o-chlorotoluene and β zeolite, which is applied in the field of nitration of organic matter, can solve the problems of environmental pollution and poor selectivity of nitrification waste acid, achieve the effects of increasing conversion rate and yield, improving reaction selectivity, and reducing the amount of waste acid treatment
- Summary
- Abstract
- Description
- Claims
- Application Information
AI Technical Summary
Problems solved by technology
Method used
Examples
Embodiment 1
[0025] Add 5mL of dichloromethane, 3.0mmol of o-chlorotoluene, 3.0mmol of acetic anhydride, 3mmol of fuming nitric acid, and 0.10g of zeolite molecular sieve Agβ catalyst (calcined at 500°C for 2h before use) into a 25mL round-bottom flask under magnetic stirring. ) and 0.1 g of silica-loaded perfluorosulfonic acid resin, heated to reflux for 4 h, added 5 mL of water to the reaction mixture to stop the reaction, filtered to remove the catalyst, and the organic phase was successively washed with 10 mL of water and 10 mL of NaHCO with a mass fraction of 5%. 3 Wash with 10mL of water and let stand to separate the organic phase. Gas chromatographic analysis was performed using p-nitrotoluene as an internal standard. The results showed that the yield was 56.3%, and the selectivity of 2-chloro-4-nitrotoluene reached 79.5%.
Embodiment 2
[0027] Under the condition of magnetic stirring, 5 mL of 1,2-dichloroethane, 3.0 mmol of o-chlorotoluene, 3.0 mmol of acetic anhydride, 6 mmol of fuming nitric acid, 0.10 g of zeolite molecular sieve Znβ catalyst and silica-supported Perfluorosulfonic acid resin 0.1g, after heating to reflux for 2h, add 5mL water to the reaction mixture to stop the reaction, filter to remove the catalyst, the organic phase is successively filled with 10mL water and 10mL NaHCO with a mass fraction of 5%. 3 Wash with 10mL of water and let stand to separate the organic phase. Gas chromatographic analysis was performed using p-nitrotoluene as an internal standard. The results showed that the yield was 74.3%, and the selectivity of 2-chloro-4-nitrotoluene reached 80.3%.
Embodiment 3
[0029] Add 5 mL of 1,2-dichloroethane, 3.0 mmol of o-chlorotoluene, 6.0 mmol of acetic anhydride, 3 mmol of fuming nitric acid, 0.10 g of zeolite molecular sieve Hβ catalyst and silica-supported Perfluorosulfonic acid resin 0.1g, after heating to reflux for 3h, add 5mL water to the reaction mixture to stop the reaction, after filtering to remove the catalyst, the organic phase is successively filled with 10mL water and 10mL NaHCO with a mass fraction of 5%. 3 Wash with 10mL of water and let stand to separate the organic phase. Gas chromatographic analysis was performed using p-nitrotoluene as an internal standard. The results showed that the yield was 67.7%, and the selectivity of 2-chloro-4-nitrotoluene reached 76.4%.
PUM
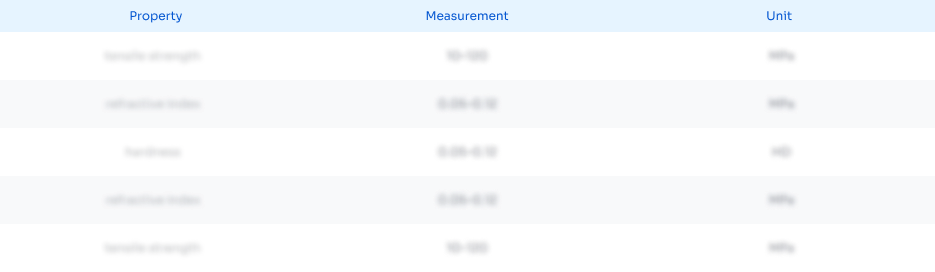
Abstract
Description
Claims
Application Information

- R&D Engineer
- R&D Manager
- IP Professional
- Industry Leading Data Capabilities
- Powerful AI technology
- Patent DNA Extraction
Browse by: Latest US Patents, China's latest patents, Technical Efficacy Thesaurus, Application Domain, Technology Topic, Popular Technical Reports.
© 2024 PatSnap. All rights reserved.Legal|Privacy policy|Modern Slavery Act Transparency Statement|Sitemap|About US| Contact US: help@patsnap.com