Yarn pressing device for auxiliary drying
A technology of yarn pressing and drying furnace, which is applied in the processing of textile materials, textiles and papermaking, and the processing of textile material carriers, etc. It can solve the problems of low drying efficiency of bobbins, and achieve the goal of improving the degree of automation and drying efficiency. Effect
- Summary
- Abstract
- Description
- Claims
- Application Information
AI Technical Summary
Problems solved by technology
Method used
Image
Examples
Embodiment Construction
[0026] In order to make the technical problems, technical solutions and beneficial effects solved by the present invention clearer, the present invention will be further described in detail below in conjunction with the accompanying drawings and embodiments. It should be understood that the specific embodiments described here are only used to explain the present invention, not to limit the present invention.
[0027] The present invention is achieved through the following technical solutions:
[0028] Such as Figure 1 to Figure 4 As shown, the yarn pressing device for auxiliary drying is characterized in that it includes a pressure yarn guiding head 2 arranged in the drying furnace 1 and drives the pressure yarn guiding head 2 to move up and down in the drying furnace 1 drive assembly, the pressure yarn diversion head 2 is provided with a yarn shaft accommodating portion 21 that is moved down for the yarn shaft 91 below it to extend into, and the pressure yarn diversion head...
PUM
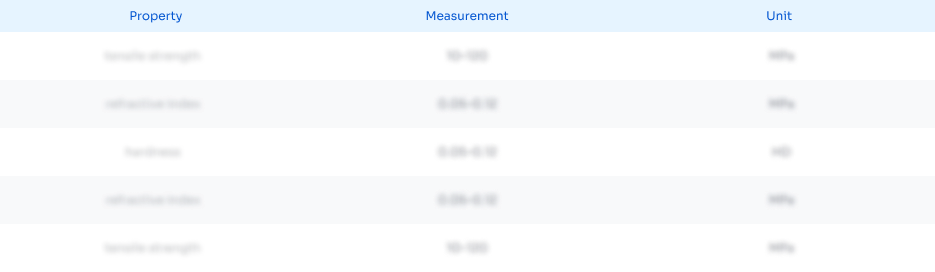
Abstract
Description
Claims
Application Information

- R&D
- Intellectual Property
- Life Sciences
- Materials
- Tech Scout
- Unparalleled Data Quality
- Higher Quality Content
- 60% Fewer Hallucinations
Browse by: Latest US Patents, China's latest patents, Technical Efficacy Thesaurus, Application Domain, Technology Topic, Popular Technical Reports.
© 2025 PatSnap. All rights reserved.Legal|Privacy policy|Modern Slavery Act Transparency Statement|Sitemap|About US| Contact US: help@patsnap.com