Flame-retardant wood-plastic composite and preparation method thereof
A wood-plastic composite material and flame retardant technology, which is applied in the field of wood-plastic composite materials, can solve the problems of complex preparation method, long time consumption, low mechanical strength and bending strength of wood-plastic composite materials, etc. Production cost, effect of good flame retardant effect
- Summary
- Abstract
- Description
- Claims
- Application Information
AI Technical Summary
Problems solved by technology
Method used
Image
Examples
Embodiment 1
[0033] 1) Weigh 15% of waste PE flakes, 16% of waste ceramic powder, STR-5301% of lubricant, 0.5% of tert-butyldiphenylchlorosilane, 10100.5% of antioxidant, and G-5060.3 of fungicide according to weight percentage %, halogen-free flame retardant 1%, ferrous ammonium sulfate 1%, polyhexamethylene biguanide 0.7%, wood fiber 64%, add to the mixer and stir evenly, the mixing temperature is 125°C, and the stirring speed is 180r / min , mixed and cooled to below 60°C to obtain a mixture;
[0034]2) Put the mixture in a twin-screw granulator for granulation to obtain wood-plastic granules. The screw speed is 250r / min, and the feeding speed is 300r / min. The temperature of each zone is controlled as follows: 150°C for zone 1, 175°C for zone 2, 180°C for zone 3, 280°C for zone 4, 280°C for zone 5, 280°C for zone 6, 280°C for zone 7, 280°C for zone 8, and 280°C for zone 9. Zone 160°C, Ten Zone 160°C;
[0035] 3) Add wood-plastic particles into a twin-screw extruder for extrusion molding...
Embodiment 2
[0037] 1) Weigh 18% of waste PE flakes, 14% of waste ceramic powder, 3% of paraffin wax, 1% of tert-butyldiphenylchlorosilane, 1680.05% of antioxidant, 0.05% of antifungal agent G-5060.05%, no Add 2% halogenated flame retardant, 1.4% ferrous ammonium sulfate, 0.5% polyhexamethylene biguanide, and 60% wood fiber into a mixer and stir evenly. The mixing temperature is 130°C and the stirring speed is 200r / min. After cooling to below 60°C to obtain the mixture;
[0038] 2) Put the mixture in a twin-screw extruder for granulation to obtain wood-plastic granules. The screw speed is 260r / min, and the feeding speed is 330r / min. The temperature of each zone is controlled as follows: Zone 1 190°C, Zone 2 195°C, Zone 3 200°C, Zone 4 260°C, Zone 5 260°C, Zone 6 260°C, Zone 7 260°C, Zone 8 260°C, Zone 9 Zone 180°C, Ten Zone 180°C;
[0039] 3) Add wood-plastic particles into a twin-screw extruder for extrusion molding to obtain a flame-retardant wood-plastic composite material. In the twi...
Embodiment 3
[0041] 1) Weigh 15% of waste PE flakes, 14.7% of waste ceramic powder, 0.5% of lubricant STR-53, 3% of tert-butyldiphenylchlorosilane, 10100.3% of antioxidant, and 0.5% of fungicide G-5060.5 according to weight percentage %, 3% halogen-free flame retardant, 2% ferrous ammonium sulfate, 1% polyhexamethylene biguanide, 60% wood fiber, add to the mixer and stir evenly, the mixing temperature is 140°C, and the stirring speed is 220r / min , mixed and cooled to below 60°C to obtain a mixture;
[0042] 2) Put the mixture in a twin-screw extruder for granulation to obtain wood-plastic granules. The screw speed is 300r / min, and the feeding speed is 400r / min. Zone, the temperature of each zone is controlled as follows: Zone 1 170°C, Zone 2 180°C, Zone 3 190°C, Zone 4 240°C, Zone 5 240°C, Zone 6 240°C, Zone 7 240°C, Zone 8 240°C, Zone 9 Zone 170°C, Ten Zone 170°C;
[0043] 3) Add wood-plastic particles into a twin-screw extruder for extrusion molding to obtain a flame-retardant wood-pla...
PUM
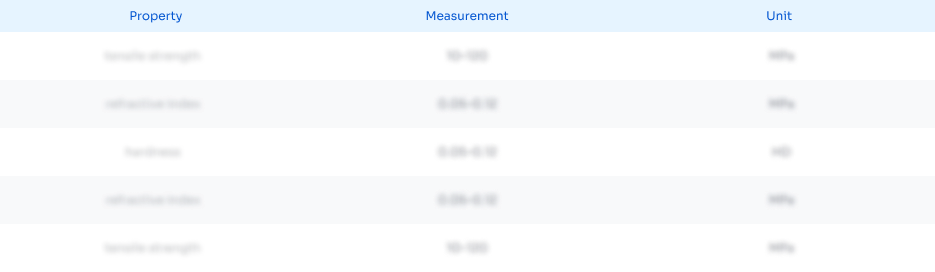
Abstract
Description
Claims
Application Information

- Generate Ideas
- Intellectual Property
- Life Sciences
- Materials
- Tech Scout
- Unparalleled Data Quality
- Higher Quality Content
- 60% Fewer Hallucinations
Browse by: Latest US Patents, China's latest patents, Technical Efficacy Thesaurus, Application Domain, Technology Topic, Popular Technical Reports.
© 2025 PatSnap. All rights reserved.Legal|Privacy policy|Modern Slavery Act Transparency Statement|Sitemap|About US| Contact US: help@patsnap.com