Lithium recovery and extraction method
A technology for extracting lithium and organic extractants, which is applied in the field of recovery and extraction of lithium elements, can solve problems such as increased sludge treatment costs, co-extraction effects, and increased post-treatment load, so as to avoid hydroxide precipitation and simplify extraction operations process, the effect of reducing post-processing load
- Summary
- Abstract
- Description
- Claims
- Application Information
AI Technical Summary
Problems solved by technology
Method used
Image
Examples
Embodiment 1
[0046] a. Add 0.2g of solid sodium hydroxide to 10ml of Cyanex272, stir the magnet and add 5ml of anhydrous ethanol and heat it to above 50°C for about three hours, and wait for the anhydrous ethanol to evaporate completely (you can compare it with the original oil level. Judging the volatilization), to obtain saponified Cyanex272;
[0047] b. Add 2g of solid sodium hydroxide to 50ml of kerosene, add 25ml of anhydrous ethanol to the magnet after stirring and heat to above 50 degrees for about three hours, wait for the absolute ethanol to evaporate completely (it can be judged by comparing with the original oil phase level (Volatilization situation), because the saturated saponified kerosene was prepared in this example, the added solid sodium hydroxide was excessive, so the saponified product was filtered through 100 mesh filter paper to remove the excess solid sodium hydroxide to obtain saturated saponified kerosene;
[0048] c. Take 1.2ml of saponified Cyanex272 and 8.8ml of satu...
Embodiment 2
[0054] a. Add 0.2g of solid sodium hydroxide to 10ml of Cyanex272, stir the magnet and add 5ml of anhydrous ethanol and heat it to above 50°C for about three hours, and wait for the anhydrous ethanol to evaporate completely (you can compare it with the original oil level. Judging the volatilization), to obtain saponified Cyanex272;
[0055] b. Add 2g of solid sodium hydroxide to 50ml of kerosene, add 25ml of anhydrous ethanol to the magnet after stirring and heat to above 50 degrees for about three hours, wait for the absolute ethanol to evaporate completely (it can be judged by comparing with the original oil phase level (Volatilization situation), because the saturated saponified kerosene was prepared in this example, the added solid sodium hydroxide was excessive, so the saponified product was filtered through 100 mesh filter paper to remove the excess solid sodium hydroxide to obtain saturated saponified kerosene;
[0056] c. Take 1.2ml of saponified Cyanex272 and 8.8ml of satu...
Embodiment 3
[0064] The difference between this embodiment and Embodiment 2 is only that the kerosene for preparing the organic solvent is changed to sulfonated kerosene.
[0065] Similarly, perform ICP (Inductively Coupled Plasma Spectrometer / Inductively Coupled Plasma Emission Spectrometer) detection on the water phase of step f, the water phase obtained by back extraction of g, and the water phase obtained by each back extraction of h to determine the content of each element. , The results are shown in Table 3.
PUM
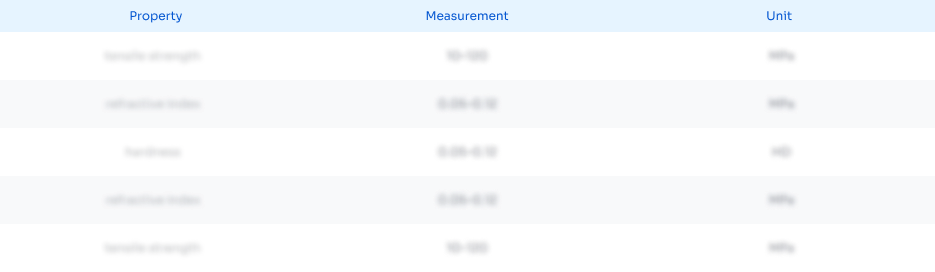
Abstract
Description
Claims
Application Information

- R&D
- Intellectual Property
- Life Sciences
- Materials
- Tech Scout
- Unparalleled Data Quality
- Higher Quality Content
- 60% Fewer Hallucinations
Browse by: Latest US Patents, China's latest patents, Technical Efficacy Thesaurus, Application Domain, Technology Topic, Popular Technical Reports.
© 2025 PatSnap. All rights reserved.Legal|Privacy policy|Modern Slavery Act Transparency Statement|Sitemap|About US| Contact US: help@patsnap.com