Gear machining process
A processing technology and gear technology, applied in the field of gear processing technology, can solve the problems of single gear material, low strength and low service life.
- Summary
- Abstract
- Description
- Claims
- Application Information
AI Technical Summary
Problems solved by technology
Method used
Image
Examples
Embodiment 1
[0023] A gear processing technology provided by the present invention is characterized in that it includes the following steps:
[0024] S1, prepare the raw materials for making gears, including the following raw materials by weight: 11 parts by weight of C, 5 parts by Cr, 950 parts by Fe, 22 parts by Mo, 6 parts by Ni, 27 parts by Ti, 14 parts by Nb, 4 parts by Be, 4 parts by Ta , Zr 4 parts, V 4 parts, W 4 parts, aluminum nitride 4 parts, rare earth elements 5.5 parts, nano-zirconium dioxide 5.5 parts, surface treatment agent 17 parts, nitrogen 65 parts;
[0025] S2: Put C, Cr, Fe, Mo, Ni, Ti, Nb, Be, Ta, Zr, V, W, aluminum nitride, rare earth elements, and nano-zirconia into the grinder and pulverize them separately. Obtain the respective powder raw materials;
[0026] S3, charge C, Cr, Fe, Mo, Ni, Ti, Nb, Be, Ta, Zr, V, W, aluminum nitride, rare earth elements and nano-zirconia powder raw materials into a high-speed mixer at a temperature of Stir and mix at a speed of 300r / min ...
Embodiment 2
[0033] A gear processing technology provided by the present invention is characterized in that it includes the following steps:
[0034] S1, prepare the raw materials for making gears, including the following raw materials by weight: 11 parts by weight of C, 5 parts by Cr, 950 parts by Fe, 22 parts by Mo, 6 parts by Ni, 27 parts by Ti, 14 parts by Nb, 4 parts by Be, 4 parts by Ta , Zr 4 parts, V 4 parts, W 4 parts, aluminum nitride 4 parts, rare earth elements 5.5 parts, nano-zirconium dioxide 5.5 parts, surface treatment agent 17 parts, nitrogen 65 parts;
[0035] S2: Put C, Cr, Fe, Mo, Ni, Ti, Nb, Be, Ta, Zr, V, W, aluminum nitride, rare earth elements, and nano-zirconia into the grinder and pulverize them separately. Obtain the respective powder raw materials;
[0036] S3, charge C, Cr, Fe, Mo, Ni, Ti, Nb, Be, Ta, Zr, V, W, aluminum nitride, rare earth elements and nano-zirconia powder raw materials into a high-speed mixer at a temperature of Stir and mix at a speed of 300r / min ...
Embodiment 3
[0043] A gear processing technology provided by the present invention is characterized in that it includes the following steps:
[0044] S1, prepare the raw materials for making gears, including the following raw materials by weight: 11 parts by weight of C, 5 parts by Cr, 950 parts by Fe, 22 parts by Mo, 6 parts by Ni, 27 parts by Ti, 14 parts by Nb, 4 parts by Be, 4 parts by Ta , Zr 4 parts, V 4 parts, W 4 parts, aluminum nitride 4 parts, rare earth elements 5.5 parts, nano-zirconium dioxide 5.5 parts, surface treatment agent 17 parts, nitrogen 65 parts;
[0045] S2: Put C, Cr, Fe, Mo, Ni, Ti, Nb, Be, Ta, Zr, V, W, aluminum nitride, rare earth elements, and nano-zirconia into the grinder and pulverize them separately. Obtain the respective powder raw materials;
[0046] S3, charge C, Cr, Fe, Mo, Ni, Ti, Nb, Be, Ta, Zr, V, W, aluminum nitride, rare earth elements and nano-zirconia powder raw materials into a high-speed mixer at a temperature of Stir and mix at a speed of 300r / min ...
PUM
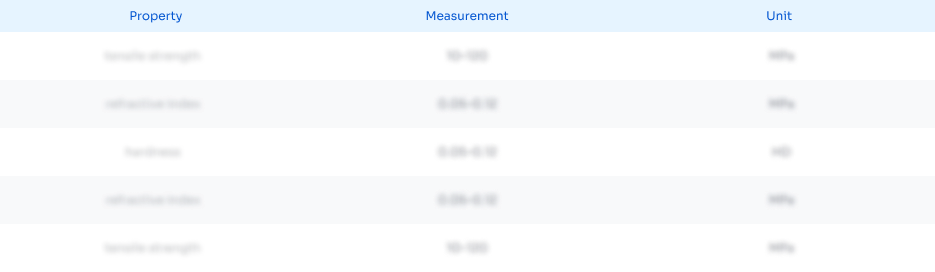
Abstract
Description
Claims
Application Information

- R&D
- Intellectual Property
- Life Sciences
- Materials
- Tech Scout
- Unparalleled Data Quality
- Higher Quality Content
- 60% Fewer Hallucinations
Browse by: Latest US Patents, China's latest patents, Technical Efficacy Thesaurus, Application Domain, Technology Topic, Popular Technical Reports.
© 2025 PatSnap. All rights reserved.Legal|Privacy policy|Modern Slavery Act Transparency Statement|Sitemap|About US| Contact US: help@patsnap.com