Ultra-precise three-coordinate testing platform
A test platform and three-coordinate technology, applied in measuring devices, instruments, etc., can solve the problems of poor dynamic performance and large deformation of the measuring machine, and achieve the effects of reducing deformation, improving rigidity and simple installation.
- Summary
- Abstract
- Description
- Claims
- Application Information
AI Technical Summary
Problems solved by technology
Method used
Image
Examples
Embodiment
[0032] Embodiment: an ultra-precise three-coordinate test platform.
[0033] refer to Figure 1 to Figure 11 As shown, an ultra-precision three-coordinate test platform includes:
[0034] The base 1, the base 1 is spliced into an "L" shape by a horizontally arranged smooth marble slab and a vertically arranged smooth marble slab, and the vertical end faces of the "L" shaped base 1 are parallel Two limit blocks 9 are arranged at intervals, a slideway is formed between the two limit blocks 9, and the surface of the marble base 1 is smooth and flat, which is conducive to the formation of a uniform air film on the surface of the vacuum preloaded air flotation component;
[0035] The support connector 3, which is arranged in a "7" shape, facilitates the support connector 3 to be in contact with the horizontal and vertical surfaces of the base 1 at the same time, and facilitates the installation of the bottom driving device and the measuring device ; The left edge and the bottom...
PUM
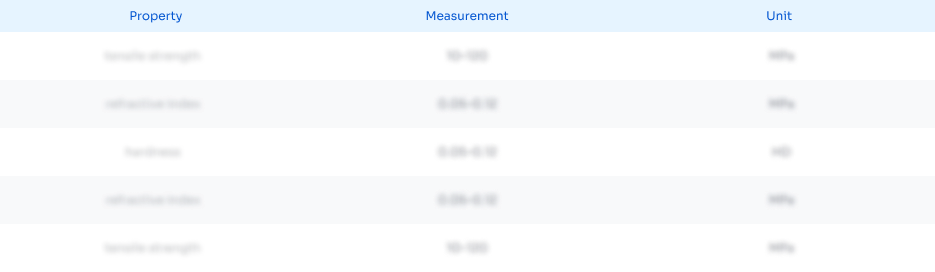
Abstract
Description
Claims
Application Information

- R&D
- Intellectual Property
- Life Sciences
- Materials
- Tech Scout
- Unparalleled Data Quality
- Higher Quality Content
- 60% Fewer Hallucinations
Browse by: Latest US Patents, China's latest patents, Technical Efficacy Thesaurus, Application Domain, Technology Topic, Popular Technical Reports.
© 2025 PatSnap. All rights reserved.Legal|Privacy policy|Modern Slavery Act Transparency Statement|Sitemap|About US| Contact US: help@patsnap.com