Acid and alkali resisting craft glass and preparation method thereof
A technology of acid and alkali resistance and glass, which is applied in the field of acid and alkali resistant craft glass and its preparation, which can solve the problems of reducing the service life of glass, achieve the effects of reducing usage, saving costs, and improving acid and alkali resistance
- Summary
- Abstract
- Description
- Claims
- Application Information
AI Technical Summary
Problems solved by technology
Method used
Examples
Embodiment 1
[0032] The acid and alkali resistant craft glass provided in this embodiment is made of the following raw materials: 55 parts of quartz sand, 8 parts of feldspar powder, 3.6 parts of asbestos segments, 9 parts of lauric acid, glass Fiber mineral powder 4.5 parts, ethyltrimethoxysilane 5 parts, amphibole powder 9.7 parts, antimony trioxide 2.5 parts, antimony oxide 13 parts.
[0033] As a preferred version, the quartz sand is obtained through the following methods:
[0034] (1) Rough selection: choose ordinary quartz sand with a silica content ≥ 98% to remove obvious impurities and foreign matter;
[0035] (2) The first calcination-water quenching: calcinate the quartz sand at 1300°C for 4 hours, then rinse the quartz sand with 4°C water for 20 seconds, then soak the quartz sand in 35°C water for 3 minutes while applying ultrasound , to crack the quartz sand;
[0036] (3) Crushing: Grind the quartz sand to 160 mesh by wet grinding or dry grinding, wash with deionized water an...
Embodiment 2
[0050] The acid and alkali resistant craft glass provided in this embodiment is made of the following raw materials: 23 parts of quartz sand, 11 parts of feldspar powder, 2 parts of asbestos segments, 11 parts of lauric acid, glass 2 parts of fiber mineral powder, 11 parts of ethyltrimethoxysilane, 3.5 parts of amphibole powder, 3.1 parts of antimony trioxide, and 2.6 parts of antimony oxide.
[0051] As a preferred version, the quartz sand is obtained through the following methods:
[0052] (1) Rough selection: choose ordinary quartz sand with a silica content ≥ 98% to remove obvious impurities and foreign matter;
[0053] (2) The first calcination-water quenching: calcinate the quartz sand at 800°C for 5 hours, then rinse the quartz sand with 0°C water for 60 seconds, then soak the quartz sand in 20°C water for 5 minutes while applying ultrasound , to crack the quartz sand;
[0054] (3) Crushing: Grind the quartz sand to 100 mesh by wet or dry grinding, wash with deionized...
Embodiment 3
[0068] The acid and alkali resistant craft glass provided in this embodiment is made of the following raw materials: 35 parts of quartz sand, 9 parts of feldspar powder, 2.8 parts of asbestos segments, 10 parts of lauric acid, glass 3.6 parts of fiber mineral powder, 7 parts of ethyltrimethoxysilane, 6.7 parts of amphibole powder, 2.9 parts of antimony trioxide, and 6 parts of antimony oxide.
[0069] As a preferred version, the quartz sand is obtained through the following methods:
[0070] (1) Rough selection: choose ordinary quartz sand with a silica content ≥ 98% to remove obvious impurities and foreign matter;
[0071] (2) The first calcination-water quenching: calcinate the quartz sand at 900°C for 4 hours, then rinse the quartz sand with 3°C water for 40 seconds, then soak the quartz sand in 25°C water for 4 minutes while applying ultrasound , to crack the quartz sand;
[0072] (3) Crushing: Grind the quartz sand to 140 mesh by wet or dry grinding, wash with deionized...
PUM
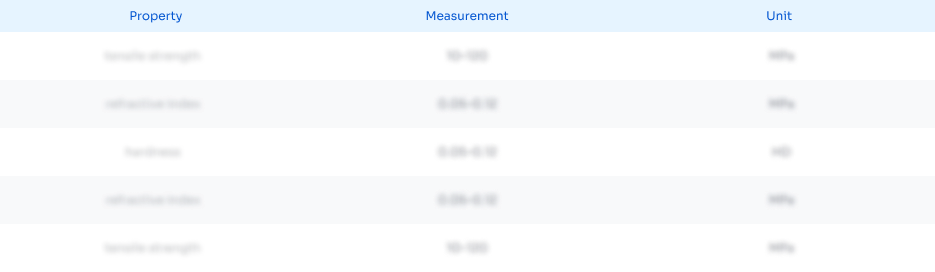
Abstract
Description
Claims
Application Information

- Generate Ideas
- Intellectual Property
- Life Sciences
- Materials
- Tech Scout
- Unparalleled Data Quality
- Higher Quality Content
- 60% Fewer Hallucinations
Browse by: Latest US Patents, China's latest patents, Technical Efficacy Thesaurus, Application Domain, Technology Topic, Popular Technical Reports.
© 2025 PatSnap. All rights reserved.Legal|Privacy policy|Modern Slavery Act Transparency Statement|Sitemap|About US| Contact US: help@patsnap.com