Built-in radial permanent magnet rotor structure
A permanent magnet rotor, permanent magnet technology, applied in the shape/style/structure of the magnetic circuit, the rotating parts of the magnetic circuit, the magnetic circuit, etc. It can reduce the magnetic flux leakage coefficient, simplify the structure and improve the starting performance.
- Summary
- Abstract
- Description
- Claims
- Application Information
AI Technical Summary
Problems solved by technology
Method used
Image
Examples
Embodiment Construction
[0023] figure 1 Among them, there are four built-in radial permanent magnet slots on the rotor punching plate 3, and 16 circular cage holes and 4 special-shaped cage holes are evenly distributed on the outer circle. The top of the 4 special-shaped cage holes is circular, The bottom is a rectangle, connected up and down. This structure integrates 4 rectangular magnetic isolation bridges and circular cage bars, which can provide a larger permanent magnet space and improve the power density of the motor. At the same time, the cage bars and the magnetic isolation bars are cast at the same time when casting aluminum. It reduces the process flow and enhances the mechanical strength of the rotor core. Four circular holes are uniformly distributed in the middle of the punching sheet, and are used for fixing the rotor punching sheet 3 and the rotor spacer 2 together through the fixing rod 4, thereby enhancing the mechanical strength of the rotor core 10. The rotor punch 3 is made of...
PUM
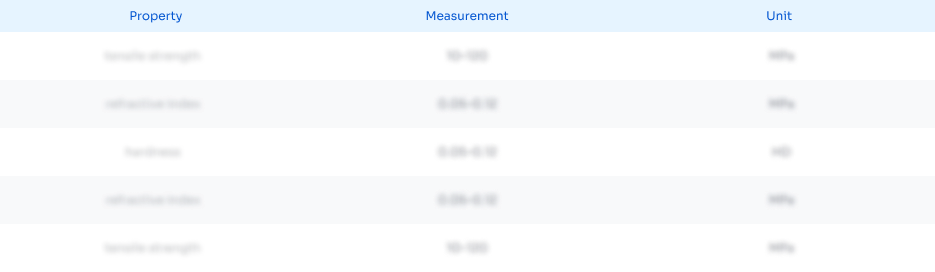
Abstract
Description
Claims
Application Information

- R&D
- Intellectual Property
- Life Sciences
- Materials
- Tech Scout
- Unparalleled Data Quality
- Higher Quality Content
- 60% Fewer Hallucinations
Browse by: Latest US Patents, China's latest patents, Technical Efficacy Thesaurus, Application Domain, Technology Topic, Popular Technical Reports.
© 2025 PatSnap. All rights reserved.Legal|Privacy policy|Modern Slavery Act Transparency Statement|Sitemap|About US| Contact US: help@patsnap.com