Flame retardant foam plastic and preparation method thereof
A foam plastic and flame-retardant technology, which is applied in the field of flame-retardant foam plastic and its preparation, can solve the problems of poor flame-retardant performance, achieve the effects of not being easy to break and drop slag, avoiding force shrinkage, and enhancing the compression resistance
- Summary
- Abstract
- Description
- Claims
- Application Information
AI Technical Summary
Problems solved by technology
Method used
Examples
Embodiment 1
[0036]Embodiment 1: A kind of flame-retardant foamed plastics, is made of the raw material of following weight parts: polystyrene 76 parts, flame retardant 12 parts, binder 5 parts, calcium stearate 6 parts, foaming agent 4 parts part, 0.5 part of talcum powder, wherein the flame retardant is mixed by mixture A and mixture B according to the mass ratio of 1:2, and mixture A is phosphate rod, tris (2-chloroethyl) phosphate and methylphosphonic acid Dimethyl ester is mixed according to the mass ratio of 2:1:1, mixture B is made of decabromodiphenylethane and magnesium hydroxide mixed according to the mass ratio of 1:2, and the adhesive is prepared by the following method Preparation: Take 3.5 parts of high-activity epoxy resin, add 0.2 parts of triethylamine to the high-activity epoxy resin at room temperature, mix well, then add 0.1 part of m-phenylenediamine, fully stir and mix evenly; The agent is formed by mixing azodicarbonamide and zinc acetate according to a mass ratio of...
Embodiment 2
[0042] Embodiment 2: a kind of flame-retardant foamed plastics, is made of the raw material of following weight parts: polystyrene 80 parts, flame retardant 14 parts, binder 6 parts, calcium stearate 7 parts, foaming agent 6 parts part, 0.6 part of talcum powder, wherein the flame retardant is mixed by mixture A and mixture B according to the mass ratio of 1:2, and mixture A is phosphoric acid rod, tris (2-chloroethyl) phosphate and methylphosphonic acid Dimethyl ester is mixed according to the mass ratio of 2:1:1, mixture B is made of decabromodiphenylethane and magnesium hydroxide mixed according to the mass ratio of 1:2, and the adhesive is prepared by the following method Preparation: Take 4.5 parts of high-activity epoxy resin, add 0.3 parts of triethylamine to the high-activity epoxy resin at room temperature, mix well, then add 0.2 parts of m-phenylenediamine, fully stir and mix evenly; The agent is formed by mixing azodicarbonamide and zinc acetate according to a mass ...
Embodiment 3
[0048] Embodiment 3: A kind of flame-retardant foamed plastics, is made of the raw material of following weight parts: polystyrene 84 parts, flame retardant 16 parts, binder 8 parts, calcium stearate 9 parts, foaming agent 8 parts Parts, 0.8 parts of talcum powder, wherein the flame retardant is mixed by mixture A and mixture B according to the mass ratio of 1:2, mixture A is phosphate rod, tris (2-chloroethyl) phosphate and methylphosphonic acid Dimethyl ester is mixed according to the mass ratio of 2:1:1, mixture B is made of decabromodiphenylethane and magnesium hydroxide mixed according to the mass ratio of 1:2, and the adhesive is prepared by the following method Preparation: Take 5.5 parts of high-activity epoxy resin, add 0.4 parts of triethylamine to the high-activity epoxy resin at room temperature, mix well, then add 0.3 parts of m-phenylenediamine, fully stir and mix evenly; The agent is formed by mixing azodicarbonamide and zinc acetate according to a mass ratio of...
PUM
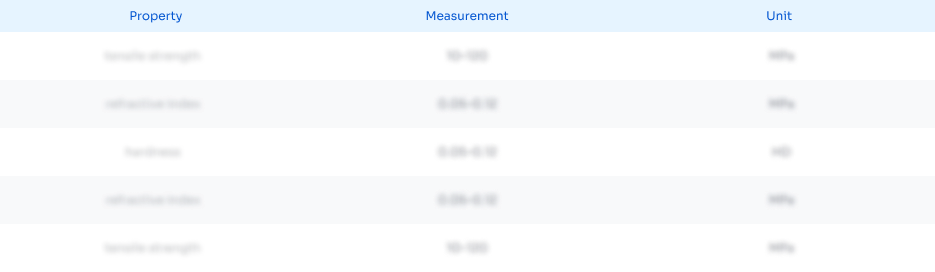
Abstract
Description
Claims
Application Information

- R&D
- Intellectual Property
- Life Sciences
- Materials
- Tech Scout
- Unparalleled Data Quality
- Higher Quality Content
- 60% Fewer Hallucinations
Browse by: Latest US Patents, China's latest patents, Technical Efficacy Thesaurus, Application Domain, Technology Topic, Popular Technical Reports.
© 2025 PatSnap. All rights reserved.Legal|Privacy policy|Modern Slavery Act Transparency Statement|Sitemap|About US| Contact US: help@patsnap.com