An integrated pipe body cutting and stacking mechanism for automobiles
A cutting mechanism and integrated technology, applied in the field of auto parts processing, can solve the problems of low cutting efficiency, inconvenient cleaning, no separation, etc., to improve the efficiency of pipe delivery, cutting efficiency, and the continuity of feeding Effect
- Summary
- Abstract
- Description
- Claims
- Application Information
AI Technical Summary
Problems solved by technology
Method used
Image
Examples
Embodiment 1
[0054] Such as figure 1 As shown, the present invention discloses an integrated pipe body cutting and stacking mechanism for automobiles, including a cutting mechanism 1 , a transfer mechanism 2 and a stacking mechanism 3 . The cutting mechanism 1 is used to cut the straight pipe 7 to be cut, and the transfer mechanism 2 is used to transport the cut straight pipes 8 to the stacking mechanism 3 for stacking.
[0055] Such as figure 1 , 2 As shown, the cutting mechanism 1 includes a first conveying device 11 , an alignment and unloading device 12 , a rotary feeding device 13 , a cutting machine 14 , a second conveying device 15 , and a leftover material separating device 16 . The first conveying device 11 is used to transport the straight pipe 7 to be cut into the alignment and unloading device 12, and the alignment and unloading device 12 is used to align the straight pipe 7 to be cut and delivered thereinto and align the aligned straight pipe 8 is unloaded into the rotary f...
Embodiment 2
[0065] Such as Figure 2-4 As shown, the difference of this embodiment compared with the above embodiments is that this embodiment provides a cutting machine 14, including a knife seat 141, a swing cutting device, and a plurality of swing cutting devices corresponding to the same feeding The cutouts 13222 on the block 1322 are in one-to-one correspondence. Each oscillating cutting device includes a cantilever 1421 and a cutting knife 1422. The lower end of the cantilever 1421 is rotatably connected to the knife seat 141 by a cutter shaft 1423, and the higher end of the cantilever 1421 is connected to the cutting knife by a knife shaft 1424. 1422 is rotationally connected, the cutter shaft 1423 is driven to rotate by the cutting motor 1425, and the cutter shaft 1424 is driven to rotate by the cutter motor 1426, preferably, between the cutter shaft 1424 and the cantilever 1421, between the knife seat 141 and the cutter shaft 1423 Bearings are set between them. The cutting knif...
Embodiment 3
[0069] The difference between this embodiment and the above embodiment is that: the cutting machine 14 further includes a cooling system, and the cooling system is used to cool the cutting blade 1422 . The cooling system includes a liquid inlet pipe (not shown in the figure), a liquid outlet pipe (not shown in the figure), and the cutter shaft 1424 is a hollow structure, such as Figure 12-14 As shown, a liquid injection channel 14221 is provided inside the cutting knife 1422 , and the liquid injection channel 14221 communicates with the inner cavity of the knife shaft 1424 . Several liquid injection channels 14221 diverge from the center of the cutting knife 1422 to the edge of the cutting knife 1422 in a radial shape. One end of the cutter shaft 1424 is provided with a liquid inlet (not shown in the figure), and the other end of the cutter shaft 1424 is provided with a liquid outlet (not shown in the figure), and a water outlet is provided at the liquid outlet and the liquid...
PUM
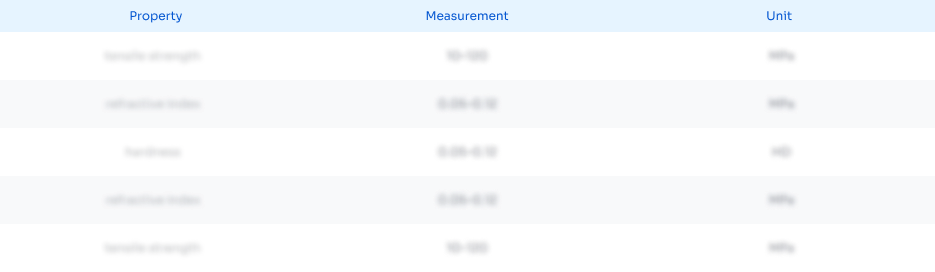
Abstract
Description
Claims
Application Information

- R&D
- Intellectual Property
- Life Sciences
- Materials
- Tech Scout
- Unparalleled Data Quality
- Higher Quality Content
- 60% Fewer Hallucinations
Browse by: Latest US Patents, China's latest patents, Technical Efficacy Thesaurus, Application Domain, Technology Topic, Popular Technical Reports.
© 2025 PatSnap. All rights reserved.Legal|Privacy policy|Modern Slavery Act Transparency Statement|Sitemap|About US| Contact US: help@patsnap.com