Precision stamping process for sheet metal parts
A technology of precision stamping and sheet metal parts, applied in metal processing equipment, forming tools, manufacturing tools, etc., can solve the difficulty of stamping, the accuracy, speed, quality and reliability of ordinary stamping can not be adapted to large-scale, large-scale, High precision, automated production, and high product precision requirements
- Summary
- Abstract
- Description
- Claims
- Application Information
AI Technical Summary
Problems solved by technology
Method used
Examples
Embodiment 1
[0027] What present embodiment selects for use is seat belt buckle, and its process comprises:
[0028] (1) Blanking: Calculate the unfolded size according to the size of the safety belt buckle, select 20# steel according to the unfolded size, and cut the plate into pieces by a shearing machine;
[0029] (2) Trimming: Flatten the sheet, trim the edges, and set positioning holes on the sheet;
[0030] (3) Preparation of graphite solvent: 4% graphite, 2.8% ethylene glycol, 10% ethanol, 1.3% ethyl acrylate, 0.9% sodium dodecylsulfonate and the rest of the water are mixed into a suspension ;
[0031] (4) Before stamping: Use a cushion under the stamping die, the material of which is silicone rubber; first heat the mold to 110-120°C, and spray ink solvent on the mold before stamping;
[0032] (5) Suction stamping: Stamping uses a stamping die, and an air suction device is arranged below the stamping die. The suction device is an air suction pump; the flow rate of the air suction ...
Embodiment 2
[0033] Embodiment 2: The present embodiment is different from Embodiment 1 in that the proportioning of the graphite solvent is: 4.5% graphite, 3% ethylene glycol, 9% ethanol, 1.2% ethyl acrylate, 1.0% ten Sodium dialkylsulfonate and the balance of water.
Embodiment 3
[0034] Embodiment 3: The present embodiment is different from Embodiment 1 in that the proportioning of graphite solvent is: 5% graphite, 2% ethylene glycol, 8% ethanol, 1.5% ethyl acrylate, 0.8% ten Sodium dialkylsulfonate and the balance of water.
PUM
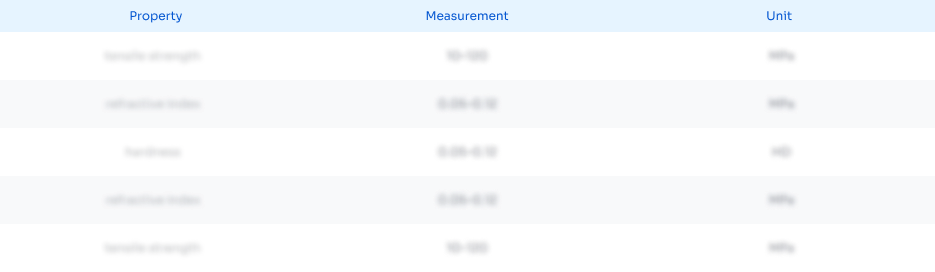
Abstract
Description
Claims
Application Information

- R&D
- Intellectual Property
- Life Sciences
- Materials
- Tech Scout
- Unparalleled Data Quality
- Higher Quality Content
- 60% Fewer Hallucinations
Browse by: Latest US Patents, China's latest patents, Technical Efficacy Thesaurus, Application Domain, Technology Topic, Popular Technical Reports.
© 2025 PatSnap. All rights reserved.Legal|Privacy policy|Modern Slavery Act Transparency Statement|Sitemap|About US| Contact US: help@patsnap.com