Activated carbon adsorption tower system and desulfurization and denitration system
An activated carbon adsorption tower, adsorption tower technology, applied in gas treatment, membrane technology, dispersed particle separation and other directions, can solve the problems of large quantity, unimaginable impact and loss, difficult maintenance and repair, etc., to improve the denitration effect and improve the purification efficiency. , to avoid the effect of repeated processing
- Summary
- Abstract
- Description
- Claims
- Application Information
AI Technical Summary
Problems solved by technology
Method used
Image
Examples
Embodiment approach
[0093] According to the first embodiment provided by the present invention, an activated carbon adsorption tower system is provided.
[0094] An activated carbon adsorption tower system. One side of the activated carbon adsorption tower 1 is provided with a first flue gas inlet A and a second flue gas inlet B. The other side of the adsorption tower 1 is provided with a first flue gas outlet C and a second flue gas outlet D. The first flue gas inlet A is arranged below the second flue gas inlet B. The first flue gas outlet C is arranged below the second flue gas outlet D. The first flue gas inlet A is connected to the original flue gas delivery pipe L1. The first flue gas outlet C is connected to the second flue gas inlet B through the first delivery pipe L2. The second flue gas outlet D is connected to the clean flue gas pipe L3. A first ammonia injection device 201 is provided at the first flue gas inlet A. A second ammonia injection device 202 is provided at the second flu...
Embodiment 1
[0108] Such as figure 2 As shown, an activated carbon adsorption tower system is provided with a first flue gas inlet A and a second flue gas inlet B on one side of the activated carbon adsorption tower 1. The other side of the adsorption tower 1 is provided with a first flue gas outlet C and a second flue gas outlet D. The first flue gas inlet A is arranged below the second flue gas inlet B. The first flue gas outlet C is arranged below the second flue gas outlet D. The first flue gas inlet A is connected to the original flue gas delivery pipe L1. The first flue gas outlet C is connected to the second flue gas inlet B through the first delivery pipe L2. The second flue gas outlet D is connected to the clean flue gas pipe L3. A first ammonia injection device 201 is provided at the first flue gas inlet A. A second ammonia injection device 202 is provided at the second flue gas inlet B. Both the first ammonia injection device 201 and the second ammonia injection device 202 ...
Embodiment 2
[0112] Such as image 3 As shown, Example 1 is repeated, except that the position of the upper part 104 of the intake flue corresponding to the activated carbon adsorption tower 1 is the upper part 101 of the adsorption tower. The position of the middle part 105 of the intake flue corresponding to the activated carbon adsorption tower 1 is the middle part 102 of the adsorption tower. The position of the lower part 106 of the intake flue corresponding to the activated carbon adsorption tower 1 is the lower part 103 of the adsorption tower. A first partition 601 is provided between the first flue gas inlet A and the second flue gas inlet B (that is, a first partition 601 is provided between the upper portion 104 of the intake flue and the middle portion 105 of the intake flue). A second partition 602 is provided between the middle portion 105 of the intake flue and the lower portion 106 of the intake flue. A third partition 603 is arranged between the first flue gas outlet C and...
PUM
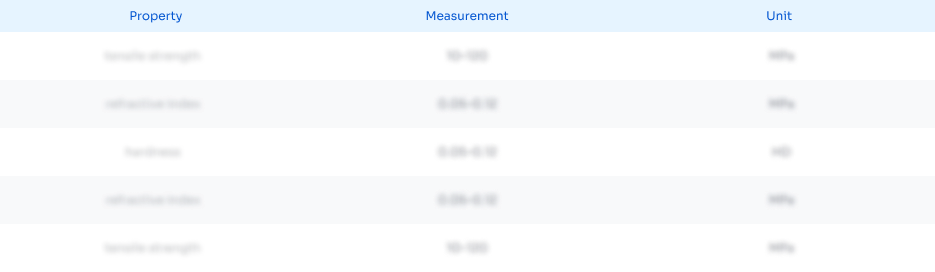
Abstract
Description
Claims
Application Information

- R&D
- Intellectual Property
- Life Sciences
- Materials
- Tech Scout
- Unparalleled Data Quality
- Higher Quality Content
- 60% Fewer Hallucinations
Browse by: Latest US Patents, China's latest patents, Technical Efficacy Thesaurus, Application Domain, Technology Topic, Popular Technical Reports.
© 2025 PatSnap. All rights reserved.Legal|Privacy policy|Modern Slavery Act Transparency Statement|Sitemap|About US| Contact US: help@patsnap.com