Integrated slurry-leaking-preventing filling material
A technology of filling materials and anti-leakage grout, which is applied in the joints of formwork/formwork/working frame, the preparation of building components on site, construction, etc., and can solve the problems of affecting the adhesiveness of the tape, low work efficiency, and adverse effects. Achieve the effects of increasing bending performance, improving work efficiency, and meeting fire resistance requirements
- Summary
- Abstract
- Description
- Claims
- Application Information
AI Technical Summary
Problems solved by technology
Method used
Image
Examples
Embodiment 1
[0032] An integrated leak-proof slurry filling material, including a base 1 and a baffle 2, the base 1 is made of XPE material as a whole, with stable chemical properties, soft and plastic materials, high tensile strength, and easy to add flame retardants to make flame retardants. The material meets the fire resistance requirements of the project. In addition, the flexibility of the XPE material can be used to fine-tune the error caused by the mismatch between the embedded channel 8 and the base to ensure the sealing of the final product after molding. And the base 1 is adapted to the internal size of the embedded channel 8, the baffle 2 is adapted to the width of the embedded channel 8, and the baffle 2 is connected to the base 1 through a connecting neck 3, and the connecting neck 3 Made of elastic material, the width of the connecting neck 3 is adapted to the opening of the embedded channel 8, the end of the base 1 away from the baffle 2 is provided with a mesh cloth 4, and ...
Embodiment 2
[0034] An integrated anti-leakage slurry filling material, comprising a base 1, a closed cavity 7 is arranged in the base 1, and a baffle 2, the base 1 is made of a flexible material and is connected to the interior of the pre-embedded channel 8. The size is adapted, the baffle 2 is adapted to the width of the embedded channel 8, the baffle 2 is connected with the base 1 through the connecting neck 3, and the side of the baffle 2 close to the base 1 is provided with a rubber magnetic sheet 5 , the width of the connecting neck 3 is adapted to the opening of the embedded channel 8 , and the end of the base 1 away from the baffle 2 is provided with a mesh cloth 4 . The rubber magnetic sheet absorbs the metal surface of the opening of the channel, in addition to having better sealing performance than the original tape, it can also prevent the original tape from being affected by the change of the maintenance environment temperature and alkaline environment, and it can also prevent ...
PUM
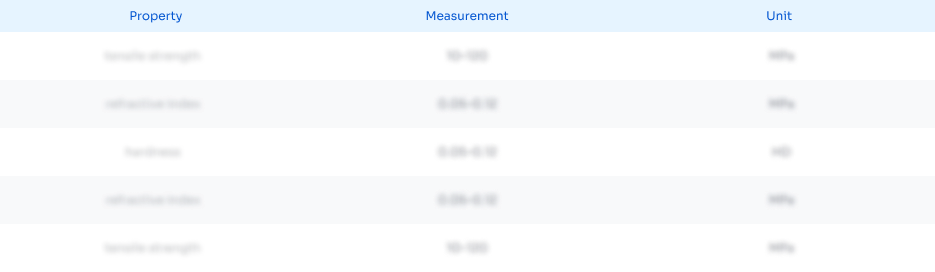
Abstract
Description
Claims
Application Information

- R&D
- Intellectual Property
- Life Sciences
- Materials
- Tech Scout
- Unparalleled Data Quality
- Higher Quality Content
- 60% Fewer Hallucinations
Browse by: Latest US Patents, China's latest patents, Technical Efficacy Thesaurus, Application Domain, Technology Topic, Popular Technical Reports.
© 2025 PatSnap. All rights reserved.Legal|Privacy policy|Modern Slavery Act Transparency Statement|Sitemap|About US| Contact US: help@patsnap.com