Cobalt black pigment for ceramic ink and preparation method of cobalt black pigment
A technology of ceramic ink and black material, which is applied in the field of ceramic materials, can solve the problems of weak hair color, strong magnetism of the color material, and pulling wires, etc., and achieve the effect of full hair color, pure color tone, and low magnetism
- Summary
- Abstract
- Description
- Claims
- Application Information
AI Technical Summary
Problems solved by technology
Method used
Examples
preparation example Construction
[0028] The present invention also provides a preparation method of the above-mentioned cobalt black material for ceramic ink, comprising the following steps:
[0029] S1. Weigh the following raw materials according to weight percentage: Co 3 O 4 35%-45%, NiO 15%-20%, Fe 2 O 3 8%-15%, Cr 2 O 3 20%-30%, in which the particle size of each raw material is D100<10um;
[0030] S2. The raw materials weighed in step S1 are mixed uniformly to obtain a reactant, and the reactant, high alumina ball stone and solvent are placed in a ball mill for ball milling treatment, so that the particle size of the reactant D100≤8um;
[0031] Wherein, the mass ratio of the reactants, the high alumina balls, and the solvent is 100:(500-550):(60-70); more preferably, the mass ratios of the reactants, the high alumina balls, and the solvent are 100:525:65.
[0032] The solvent is preferably water, but not limited thereto.
[0033] In the ball milling of the present invention, the rotation of t...
Embodiment 1
[0043]A kind of cobalt black material for ceramic ink, its preparation method is:
[0044] S1. Weigh the following raw materials according to weight percentage: Co 3 O 4 40%, NiO 18%, Fe 2 O 3 15%, Cr 2 O 3 27%; the particle size D100 of the above raw materials is less than 10um;
[0045] S2. The raw materials weighed in step S1 are mixed uniformly to obtain the reactant, and the reactant, high alumina ball stone and water are placed in a ball mill for ball milling treatment, so that the particle size of the reactant D100≤8um; wherein, the reactant, The mass ratio of high alumina ball stone and solvent is 100:525:65; the lining of the ball mill used is a ceramic lining;
[0046] S3. The reactant is dried;
[0047] S4. calcining the material obtained in step S3, the calcining temperature is 1280°C-1320°C, and the temperature is kept for 2-3 hours;
[0048] S5. After the calcined product is subjected to crushing treatment, the ball mill is used for ultra-fine treatmen...
Embodiment 2
[0050] A kind of cobalt black material for ceramic ink, its preparation method is:
[0051] S1. Weigh the following raw materials according to weight percentage: Co 3 O 4 42%, NiO 20%, Fe 2 O 3 8%, Cr 2 O 3 30%; the particle size D100 of the above raw materials is less than 10um;
[0052] S2. The raw materials weighed in step S1 are mixed uniformly to obtain the reactant, and the reactant, high alumina ball stone and water are placed in a ball mill for ball milling treatment, so that the particle size of the reactant D100≤8um; wherein, the reactant, The mass ratio of high alumina ball stone and solvent is 100:500:70; the lining of the ball mill used is a ceramic lining;
[0053] S3. The reactant is dried;
[0054] S4. calcining the material obtained in step S3, the calcining temperature is 1280°C-1320°C, and the temperature is kept for 2-3 hours;
[0055] S5. After the calcined product is subjected to crushing treatment, the ball mill is used for ultra-fine treatment...
PUM
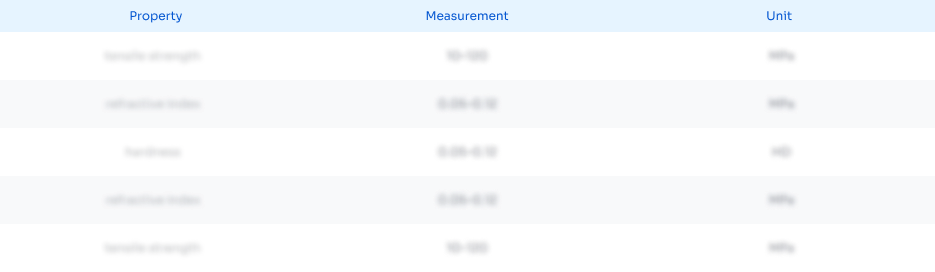
Abstract
Description
Claims
Application Information

- Generate Ideas
- Intellectual Property
- Life Sciences
- Materials
- Tech Scout
- Unparalleled Data Quality
- Higher Quality Content
- 60% Fewer Hallucinations
Browse by: Latest US Patents, China's latest patents, Technical Efficacy Thesaurus, Application Domain, Technology Topic, Popular Technical Reports.
© 2025 PatSnap. All rights reserved.Legal|Privacy policy|Modern Slavery Act Transparency Statement|Sitemap|About US| Contact US: help@patsnap.com