Pressure control system for multi-punching-die co-production
A stamping die and joint production technology, applied in the field of stamping dies, can solve the problems of unstable working gap, long mold research and repair time, cost waste of mold manufacturing enterprises and automobile stamping factories, etc., to improve production stability and production High efficiency, reduced mold grinding and mold repair time, and stable forming gap
- Summary
- Abstract
- Description
- Claims
- Application Information
AI Technical Summary
Problems solved by technology
Method used
Image
Examples
Embodiment Construction
[0016] The pressure control system for the joint production of multiple stamping dies is as follows: figure 1 and 2 As shown, it includes a press and a plurality of stamping positions arranged on the press. At least two of these stamping positions are respectively equipped with stamping dies with different pressure ranges. There are elastic elements 5, and the elastic range of these elastic elements 5 can be adjusted so that each stamping die is stamped and formed together under the control of the press machine. One of the upper mold 3 and the lower mold 4 uses an elastic element 5 as a pressure source, and the force provided by the elastic element 5 should be slightly greater than the product forming force of the current stamping position. The elastic element 5 can be as follows: figure 1 The design shown in is on the mold, and the elastic element 5 is arranged on the side of the stamping die for placing the tablet, that is, the elastic element 5 is arranged on the bottom of...
PUM
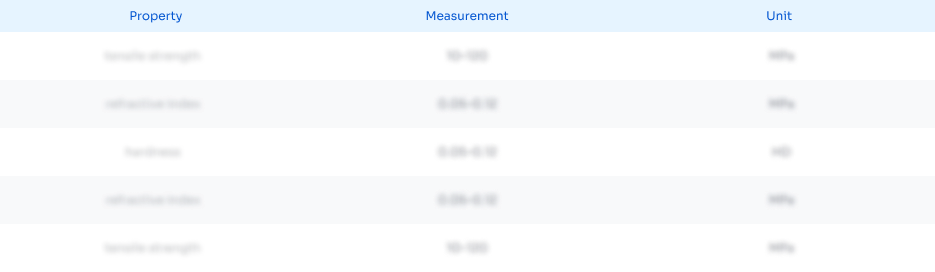
Abstract
Description
Claims
Application Information

- R&D Engineer
- R&D Manager
- IP Professional
- Industry Leading Data Capabilities
- Powerful AI technology
- Patent DNA Extraction
Browse by: Latest US Patents, China's latest patents, Technical Efficacy Thesaurus, Application Domain, Technology Topic, Popular Technical Reports.
© 2024 PatSnap. All rights reserved.Legal|Privacy policy|Modern Slavery Act Transparency Statement|Sitemap|About US| Contact US: help@patsnap.com