Casting-molded thermal-insulation nanocomposite with high-temperature resistance and preparation method of casting-molded thermal-insulation nanocomposite
A technology for nano-insulation and composite materials, which is applied in the field of casting and forming high-temperature-resistant nano-insulation composite materials and its preparation, can solve the problem that it is difficult to meet the higher requirements of performance insulation materials, and it is difficult to have high temperature resistance, low thermal conductivity and low cost at the same time. High strength and other problems, to achieve the effect of reducing solid state heat conduction, inhibiting gaseous heat conduction, and reducing radiant heat conduction
- Summary
- Abstract
- Description
- Claims
- Application Information
AI Technical Summary
Problems solved by technology
Method used
Image
Examples
Embodiment 1
[0051] The difference between the preparation process of Example 1 and Example 2-479 is that the mass fraction of each substance is different and the types of additives, opacifiers and chopped fibers are different. The details are listed in Table 1. The performance of the prepared nano-insulation composite material is as follows Table 1 shows.
[0052] It can be seen from Table 1 that the main factor affecting the compressive strength is the mass fraction of white cement. With the increase of the mass fraction of white cement, the compressive strength of the material also increases. When the white cement is 20%wt, different fiber types are compressed. The strength (10% deformation) reaches the maximum, which is 0.78-0.82MPa. The main factor affecting the thermal conductivity of the material is the mass fraction of fumed silicon oxide. As the mass fraction of fumed silicon oxide increases, the thermal conductivity of the material decreases. When the fumed silica is 30%wt, the ...
PUM
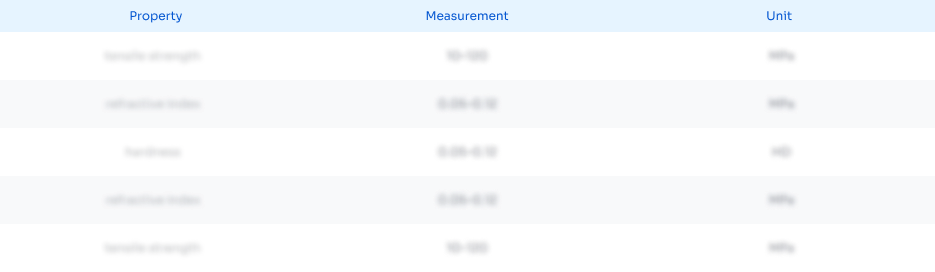
Abstract
Description
Claims
Application Information

- R&D
- Intellectual Property
- Life Sciences
- Materials
- Tech Scout
- Unparalleled Data Quality
- Higher Quality Content
- 60% Fewer Hallucinations
Browse by: Latest US Patents, China's latest patents, Technical Efficacy Thesaurus, Application Domain, Technology Topic, Popular Technical Reports.
© 2025 PatSnap. All rights reserved.Legal|Privacy policy|Modern Slavery Act Transparency Statement|Sitemap|About US| Contact US: help@patsnap.com