Method for preparing vapor-phase coated modified lithium nickelate, cobaltate and manganate positive electrode materials
A technology of nickel cobalt lithium manganate and cathode material, applied in battery electrodes, electrical components, circuits, etc., can solve the problems of cycle performance and specific capacity discount, high cost, unsatisfactory performance, etc., to improve cycle performance and The effect of processing performance, reducing input cost and improving production efficiency
- Summary
- Abstract
- Description
- Claims
- Application Information
AI Technical Summary
Problems solved by technology
Method used
Image
Examples
Embodiment 1
[0019] S1. Put the anhydrous acetic acid liquid in an anti-corrosion boiler and heat it to 120°C to boil, then transport the acetic acid vapor to the air inlet of the pneumatic mixer through the pipeline, and keep the air inlet pressure at 0.85Mpa;
[0020] S2. Take by weighing 1000Kg of conventional nickel-cobalt-manganese lithium manganese oxide (market purchase), the ratio of nickel-cobalt-manganese is nickel: cobalt: manganese=6:2:2, place in the pulse type pneumatic mixer, open the pneumatic mixer, mixing time For 5 minutes, keep the internal pressure of the mixer at +0.02Mpa, and obtain the semi-finished nickel-cobalt-lithium-manganate oxide after discharging;
[0021] S3. Place the coated semi-finished product in step S2 in a roller kiln, and raise the temperature to 750° C. for 10 hours at a heating rate of 5° C. / min;
[0022] S4. The sintered product in step S3 is subjected to mechanical grinding, screening, and iron removal to obtain the product.
Embodiment 2
[0026] S1. Put the anhydrous acetic acid liquid in an anti-corrosion boiler and heat it to 120°C to boil, then transport the acetic acid vapor to the air inlet of the pneumatic mixer through the pipeline, and keep the air inlet pressure at 0.85Mpa;
[0027] S2. Take by weighing 1000Kg of conventional nickel-cobalt lithium manganese oxide (market purchase), the ratio of nickel-cobalt-manganese is nickel: cobalt: manganese=5:2:3, place in the pulse type pneumatic mixer, open the pneumatic mixer, mixing time For 3 minutes, keep the internal pressure of the mixer at +0.02Mpa, and obtain the semi-finished nickel-cobalt-lithium-manganese oxide after discharging;
[0028] S3. Place the coated semi-finished product in step S2 in a roller kiln, and raise the temperature to 800° C. for 12 hours at a heating rate of 4° C. / min;
[0029] S4. The sintered product in step S3 is subjected to mechanical grinding, screening, and iron removal to obtain the product.
Embodiment 3
[0033] S1. Put the anhydrous acetic acid liquid in an anti-corrosion boiler and heat it to 120°C to boil, then transport the acetic acid vapor to the air inlet of the pneumatic mixer through the pipeline, and keep the air inlet pressure at 0.85Mpa;
[0034] S2. Take by weighing 1000Kg of conventional nickel-cobalt-manganese lithium manganese oxide (market purchase), the ratio of nickel-cobalt-manganese is nickel: cobalt: manganese=8:1:1, place in the pulse type pneumatic mixer, open the pneumatic mixer, mixing time For 10 minutes, keep the internal pressure of the mixer at +0.02Mpa, and discharge the coated nickel-cobalt-lithium-manganese-oxide semi-finished product;
[0035] S3. Place the coated semi-finished product in step S2 in a roller kiln, and raise the temperature to 650° C. for 8 hours at a heating rate of 3° C. / min;
[0036] S4. The sintered product in step S3 is subjected to mechanical grinding, screening, and iron removal to obtain the product.
PUM
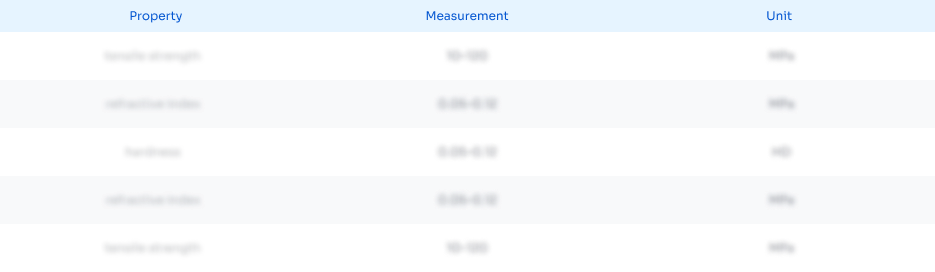
Abstract
Description
Claims
Application Information

- R&D Engineer
- R&D Manager
- IP Professional
- Industry Leading Data Capabilities
- Powerful AI technology
- Patent DNA Extraction
Browse by: Latest US Patents, China's latest patents, Technical Efficacy Thesaurus, Application Domain, Technology Topic, Popular Technical Reports.
© 2024 PatSnap. All rights reserved.Legal|Privacy policy|Modern Slavery Act Transparency Statement|Sitemap|About US| Contact US: help@patsnap.com