Method for preparing self-lubricating composite membrane layer on surface of titanium alloy drill rod through two-step method
A technology of composite film layer and titanium alloy, which is applied to the device for coating liquid on the surface, pretreatment surface, coating and other directions, can solve the problem of poor wear resistance of titanium alloy drill pipe, poor bonding force of copper plating layer, and hardness of film layer. problems such as low friction, to achieve the effect of low friction coefficient, time saving and simple process conditions
- Summary
- Abstract
- Description
- Claims
- Application Information
AI Technical Summary
Problems solved by technology
Method used
Examples
Example Embodiment
Specific implementation manner two:
[0015] The two-step method for preparing a self-lubricating composite film on the surface of a titanium alloy drill pipe includes the following steps: (1) Pretreatment of the sample surface, using sandpaper to polish the surface of the titanium alloy drill pipe sample, and then using an acetone solution in ultrasonic waves In the washer, the sample was cleaned and degreasing for 15 minutes, rinsed with deionized water, and dried with a hair dryer. (2) Prepare electrolyte, the total volume of electrolyte is 3L, the solvent is deionized water, the content of solute is: Na 2 SiO 3 :2g / L; Glycerol: 5g / L; (NaPO 3 ) 6 : 8g / L. And set the micro-arc oxidation process parameters: the current density is 10A / dm 2 , The duty cycle is 60%, the oxidation time is 10min; the frequency is 600Hz. At the same time, control the temperature of the electrolyte at 25°C. Then the titanium alloy drill pipe sample is connected to the anode and immersed in the electr...
Example Embodiment
Specific implementation manner two:
[0016] The two-step method for preparing a self-lubricating composite film on the surface of a titanium alloy drill pipe includes the following steps: (1) Pretreatment of the sample surface, using sandpaper to polish the surface of the titanium alloy drill pipe sample, and then using an acetone solution in ultrasonic waves In the washer, the sample was cleaned and degreasing for 15 minutes, rinsed with deionized water, and dried with a hair dryer. (2) Prepare electrolyte, the total volume of electrolyte is 3L, the solvent is deionized water, the content of solute is: Na 2 SiO 3 :10g / L; Glycerol: 1g / L; (NaPO 3 ) 6 : 1g / L. And set the micro-arc oxidation process parameters: the current density is 2A / dm 2 , The duty cycle is 20%, the oxidation time is 60min; the frequency is 100Hz. At the same time, control the temperature of the electrolyte at 30°C. Then the titanium alloy drill pipe sample is connected to the anode and immersed in the electr...
Example Embodiment
Specific implementation manner three:
[0017] The two-step method for preparing a self-lubricating composite film on the surface of a titanium alloy drill pipe includes the following steps: (1) Pretreatment of the sample surface, using sandpaper to polish the surface of the titanium alloy drill pipe sample, and then using an acetone solution in ultrasonic waves In the washer, the sample was cleaned and degreasing for 15 minutes, rinsed with deionized water, and dried with a hair dryer. (2) Prepare electrolyte, the total volume of electrolyte is 3L, the solvent is deionized water, the content of solute is: Na 2 SiO 3 :5g / L; Glycerol: 5g / L; (NaPO 3 ) 6 : 8g / L. And set the micro-arc oxidation process parameters: the current density is 8A / dm 2 , Duty cycle is 50%, oxidation time is 40min; frequency is 500Hz. At the same time, control the temperature of the electrolyte at 28°C. Then the titanium alloy drill pipe sample is connected to the anode and immersed in the electrolyte, the ...
PUM
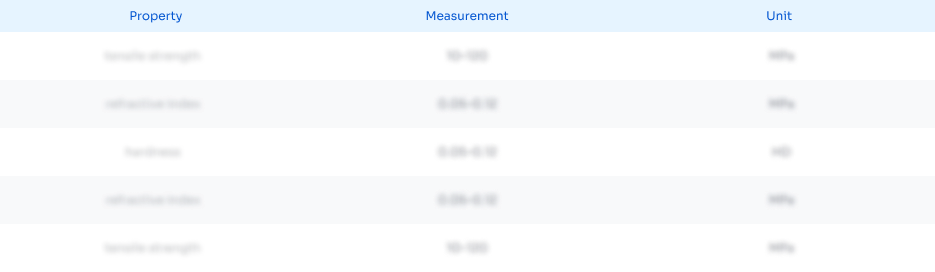
Abstract
Description
Claims
Application Information

- Generate Ideas
- Intellectual Property
- Life Sciences
- Materials
- Tech Scout
- Unparalleled Data Quality
- Higher Quality Content
- 60% Fewer Hallucinations
Browse by: Latest US Patents, China's latest patents, Technical Efficacy Thesaurus, Application Domain, Technology Topic, Popular Technical Reports.
© 2025 PatSnap. All rights reserved.Legal|Privacy policy|Modern Slavery Act Transparency Statement|Sitemap|About US| Contact US: help@patsnap.com