Plastic color matching process
A process and plastic technology, applied in the field of plastic color matching process, can solve the problems of high economic and technical requirements, poor color matching effect, uncontrollable degree of change, etc., to avoid waste of raw materials and production time, shorten process time, and save raw materials cost effect
- Summary
- Abstract
- Description
- Claims
- Application Information
AI Technical Summary
Problems solved by technology
Method used
Image
Examples
Embodiment 1
[0032] A plastic color matching process, comprising the following steps:
[0033] (1) Mixing samples: Weigh the plastic particles and add them to the high mixer, then add the dispersant and pigment and mix them evenly to get the sample; after mixing in the high mixer, put the samples into polyethylene bags and blow them with nitrogen Sweep the high mixer, put the remaining material on the bag wall into the bag; inflate the polyethylene bag, and then manually mix for about 30 seconds, and the sample is mixed by now.
[0034] (2) Multiple groups are set: 4 groups are set according to the process of step (1), the concentration of each group of dispersants is the same, and the concentration of each group of pigments is different, forming 5 kinds of pigments with different concentrations;
[0035] (3) Test the uniformity of a single group of samples: Use X-Rite’s color measuring and matching instrument Ci7800 to test the mixing uniformity of each group of samples. The special tool ...
Embodiment 2
[0044] A plastic color matching process, same as embodiment 1.
[0045] The pigment described in this embodiment is a purple pigment, the base material is 1 kg, and the color matching effects are listed in Table 2.
[0046] Table 2: Color matching effect of Example 2.
[0047]
[0048] Since injection molding needs to be melted at high temperature, partial oxidation of mixed slices is inevitable during the process, so the color matching effect after injection molding is generally worse than that of mixed slices, so it is even more necessary to avoid high temperature steps for samples as much as possible. The process of the present invention only undergoes one injection molding, and the uniformity of color matching can be well monitored and controlled through the early detection and color matching process, avoiding the occurrence of uneven color matching, and at the same time avoiding the occurrence of uneven color matching as in conventional technologies Finally, the redun...
PUM
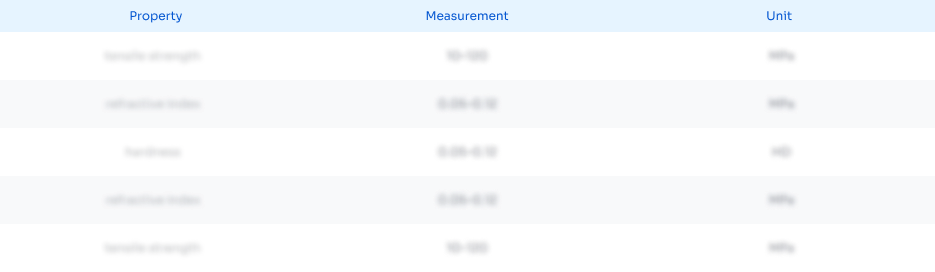
Abstract
Description
Claims
Application Information

- R&D
- Intellectual Property
- Life Sciences
- Materials
- Tech Scout
- Unparalleled Data Quality
- Higher Quality Content
- 60% Fewer Hallucinations
Browse by: Latest US Patents, China's latest patents, Technical Efficacy Thesaurus, Application Domain, Technology Topic, Popular Technical Reports.
© 2025 PatSnap. All rights reserved.Legal|Privacy policy|Modern Slavery Act Transparency Statement|Sitemap|About US| Contact US: help@patsnap.com