A Compensation Method for Motor Driving PWM Dead Zone
A compensation method and motor drive technology, applied in the field of motor compensation control and motor, can solve the problems of poor stability, low measurement accuracy, limited application of a single method, and achieve the effect of sufficient compensation and reduced requirements.
- Summary
- Abstract
- Description
- Claims
- Application Information
AI Technical Summary
Problems solved by technology
Method used
Image
Examples
Embodiment Construction
[0019] Take a 30kW pure electric drive motor as an example:
[0020] Step 1. Measure the turn-on and turn-off time of a transistor switch such as an IGBT under different voltages and currents, and use it as the basis of the dead time. The typical selection is 5 microseconds.
[0021] In step 1, when the IGBT is in the off state, the voltage is the power supply voltage, and the current is 0, and in the on state, the voltage is the conduction voltage drop, and the current is the load current. So step 1 is to test the time from turn-off to turn-on, and the time from turn-on to turn-off under different combinations of power supply voltage and load current. Just choose a meaningful combination of voltage and current (such as 300V 100A).
[0022] Step 2, measuring the change of the duty cycle of the PWM waveform under the conditions of different motor speeds, different output torques, and different voltages and currents.
[0023] The PWM waveform duty cycle in step 2 is a percenta...
PUM
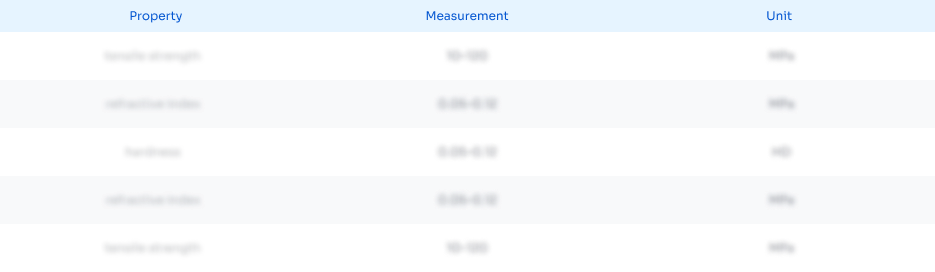
Abstract
Description
Claims
Application Information

- Generate Ideas
- Intellectual Property
- Life Sciences
- Materials
- Tech Scout
- Unparalleled Data Quality
- Higher Quality Content
- 60% Fewer Hallucinations
Browse by: Latest US Patents, China's latest patents, Technical Efficacy Thesaurus, Application Domain, Technology Topic, Popular Technical Reports.
© 2025 PatSnap. All rights reserved.Legal|Privacy policy|Modern Slavery Act Transparency Statement|Sitemap|About US| Contact US: help@patsnap.com