Layer-by-layer injection molding structure
A mold forming and injection molding technology, which is applied in the field of layer-by-layer injection mold forming structure, can solve problems such as cracks, low injection molding rate, air bubbles, etc., and achieve the effect of improving the success rate and fully compensating
- Summary
- Abstract
- Description
- Claims
- Application Information
AI Technical Summary
Problems solved by technology
Method used
Image
Examples
Embodiment Construction
[0014] Below in conjunction with embodiment the present invention is further described:
[0015] like figure 1 , figure 2 and image 3 As shown in the embodiment, this layer-by-layer injection mold molding structure includes an injection molding table 1 with an upper plane level, and the upper part of the injection molding table 1 is equipped with a lifting block 2 and a lifting ring 3, and the lifting ring 3 is wrapped in the lifting ring 3. Outside the block 2, there is a gap between the inner wall of the lifting ring 3 and the outer wall of the lifting block 2 to form an injection molding cavity. The lifting block 2 and the lifting ring 3 are fixedly connected through the upper part, and the upper part of the lifting block 2 is assembled There is a transmission module 4, the bottom of the transmission module 4 is equipped with a screw rod 41 that can rotate vertically from the axis, and a vertical screw hole is installed in the middle of the lifting block 2, and the scre...
PUM
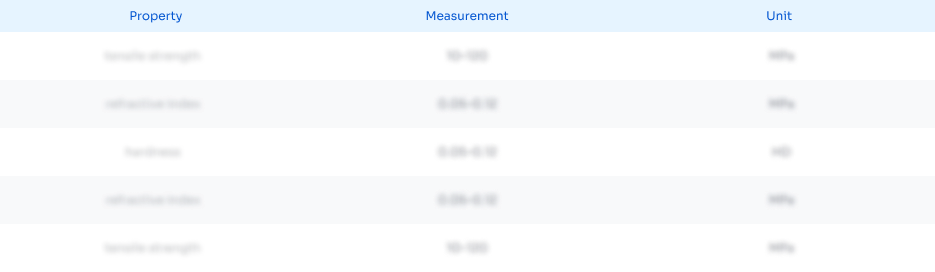
Abstract
Description
Claims
Application Information

- Generate Ideas
- Intellectual Property
- Life Sciences
- Materials
- Tech Scout
- Unparalleled Data Quality
- Higher Quality Content
- 60% Fewer Hallucinations
Browse by: Latest US Patents, China's latest patents, Technical Efficacy Thesaurus, Application Domain, Technology Topic, Popular Technical Reports.
© 2025 PatSnap. All rights reserved.Legal|Privacy policy|Modern Slavery Act Transparency Statement|Sitemap|About US| Contact US: help@patsnap.com