A kind of method for improving the yield of reverse flotation iron concentrate while reducing the consumption of caustic soda
An iron concentrate and reverse flotation technology, which is applied in chemical instruments and methods, wet separation, solid separation, etc., can solve the problems of consumption of reverse flotation reagents, drop of pH value of water body, unfavorable mineral processing operation, etc. The effect of improving ore filtration efficiency, eliminating carbonation, and saving caustic soda consumption
- Summary
- Abstract
- Description
- Claims
- Application Information
AI Technical Summary
Problems solved by technology
Method used
Image
Examples
Embodiment 1
[0063] Embodiment 1: Get the incoming water (pH value is 10.7) of the big well of floating tail on the spot, add the calcium oxide of 100ppm, stir for 1 minute, then add the PAM of 3ppm, stir for 1 minute, leave standstill for 5 minutes, clarification layer accounts for 2% of the total amount 71%, ss 125 mg / l, pH 11.8.
Embodiment 2
[0065] Embodiment 2: get the incoming water (pH value is 9.1) of the big well before the field strong magnetic field, add the calcium oxide of 50ppm, add the PAM of 3ppm again, stir 1 minute, leave standstill 5 minutes, clarification layer accounts for 78% of total amount %, ss is 112 mg / L, and its pH value is 11.1.
Embodiment 3
[0067] Embodiment 3: get water treatment unit upstream and mix into water (pH value is 9.0), add the calcium oxide of 50ppm, add the PAM of 3ppm again, stir 1 minute, leave standstill 5 minutes, clarification layer accounts for 83% of total amount, ss is 101 mg / L, its pH value is 11.1.
PUM
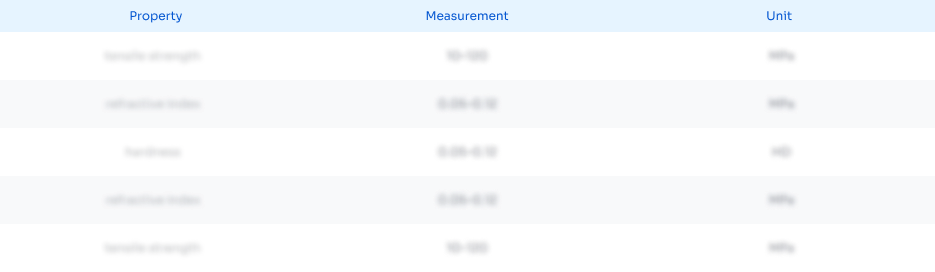
Abstract
Description
Claims
Application Information

- R&D Engineer
- R&D Manager
- IP Professional
- Industry Leading Data Capabilities
- Powerful AI technology
- Patent DNA Extraction
Browse by: Latest US Patents, China's latest patents, Technical Efficacy Thesaurus, Application Domain, Technology Topic, Popular Technical Reports.
© 2024 PatSnap. All rights reserved.Legal|Privacy policy|Modern Slavery Act Transparency Statement|Sitemap|About US| Contact US: help@patsnap.com