A comprehensive utilization method of vanadium-containing leaching solution for removing silicon waste slag
A technology for leachate and silicon waste residue, which is applied in the fields of chemical technology and waste resource utilization, can solve the problems of removing silicon waste residue and pollute the environment, and achieve the effect of improving the recovery rate
- Summary
- Abstract
- Description
- Claims
- Application Information
AI Technical Summary
Problems solved by technology
Method used
Image
Examples
Embodiment 1
[0066] A preparation method of vanadium-containing solution, comprising the steps of:
[0067] Weigh 1.5t of silicon removal waste residue (moisture 35%), add 98% sulfuric acid, slurry with liquid-solid ratio 2.6:1, temperature 60°C, control the reaction termination acid concentration 3.2g / L, stir and leaching for 2 hours, and press through the plate and frame The filter is filtered, and the filter residue can be transported to the refractory material factory to produce clay bricks. After the pickling liquid is filtered through the high-molecular PE microporous tube, the ammonium nitrogen in the supernatant liquid of high-purity ammonium metavanadate crystallization is added to prepare the ammonium sulfate solution (NH 4 ) 2 SO 4 , pH is 2.5, concentration is 330g / L, NH 4 + :Al 3+ (Molar ratio) = 1.2:1, pH = 1.5, temperature 60°C, then stir and cool down to 15°C, use a centrifuge to separate and wash, and dry to obtain NH 4 Al(SO 4 ) 2 12H 2 O. Residual Al in mother ...
Embodiment 2
[0069] A preparation method of vanadium-containing solution, comprising the steps of:
[0070] Weigh 1.5t of silicon removal waste residue (moisture 35%), add 98% sulfuric acid, slurry with a liquid-solid ratio of 3:1, temperature 60°C, control the acid concentration at the end of the reaction to 2.8g / L, stir and leaching for 2 hours, and then press through the plate and frame The filter is filtered, and the filter residue can be transported to the refractory material factory to produce clay bricks. After the pickling liquid is filtered through the high-molecular PE microporous tube, the ammonium nitrogen in the supernatant liquid of high-purity ammonium metavanadate crystallization is added to prepare the ammonium sulfate solution (NH 4 ) 2 SO 4 , the pH is 1.5, the concentration is 366g / L, the reaction control NH 4 + :Al 3+ (molar ratio) = 1.24:1, pH = 2, temperature 65°C, then stir and cool down to 12°C, use a centrifuge to separate and wash, and dry to obtain NH 4 Al...
Embodiment 3
[0072] A preparation method of vanadium-containing solution, comprising the steps of:
[0073] Weigh 1.5t of silicon removal waste residue (moisture 35%), slurry with liquid-solid ratio 3.2:1, add 98% sulfuric acid, temperature 60°C, control the reaction termination acid concentration 3.8g / L, stir and leaching for 2 hours, press through plate and frame The filter is filtered, and the filter residue can be transported to the refractory material factory to produce clay bricks. After the pickling liquid is filtered through the high-molecular PE microporous tube, the ammonium nitrogen in the supernatant liquid of high-purity ammonium metavanadate crystallization is added to prepare the ammonium sulfate solution (NH 4 ) 2 SO 4 , pH is 1.0, concentration is 360g / L, reaction control NH 4 + :Al 3+ (Molar ratio) = 1.26:1, pH = 2, temperature 55°C, then stir and cool down to 15°C, use a centrifuge to separate and wash, and dry to obtain NH 4 Al(SO 4 ) 2 12H 2 O. Residual Al in...
PUM
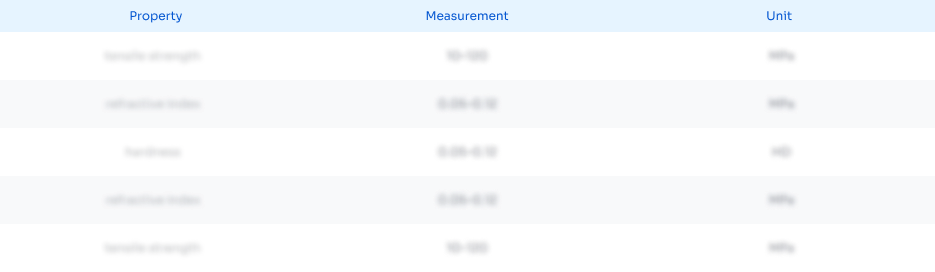
Abstract
Description
Claims
Application Information

- R&D
- Intellectual Property
- Life Sciences
- Materials
- Tech Scout
- Unparalleled Data Quality
- Higher Quality Content
- 60% Fewer Hallucinations
Browse by: Latest US Patents, China's latest patents, Technical Efficacy Thesaurus, Application Domain, Technology Topic, Popular Technical Reports.
© 2025 PatSnap. All rights reserved.Legal|Privacy policy|Modern Slavery Act Transparency Statement|Sitemap|About US| Contact US: help@patsnap.com