High-pressure forming method
一种高压、成形机的技术,应用在流体压力致动装置、流体压力致动系统组件、机械设备等方向,能够解决不能实现脉动方式加载等问题,达到提高能量利用效率、提高稳定性、保证压力的效果
- Summary
- Abstract
- Description
- Claims
- Application Information
AI Technical Summary
Problems solved by technology
Method used
Image
Examples
Embodiment 1
[0039] This embodiment is internal high pressure forming with conventional linear loading of bulging pressure, combined with Figure 1-6 This embodiment will be described.
[0040] A small and medium-sized internal high pressure forming machine with bulging pressure pulsation loading according to the present invention, comprising: an upper beam 1, four guide columns 2, two fast cylinders 3, a main cylinder 4, a movable beam 5, an upper mold 6, two (or three) axial feed cylinder 8 and the same number of punches 7, workbench 9, frame 10, lower die 11, lower cylinder 12, electrical control cabinet 13, PLC (including AD / DA module) 14. Servo driver 15, multiple button switches 16, control panel 17, touch screen 18, low-pressure liquid filling system 19, host hydraulic system 20, system oil pipe 21, booster cylinder 22, pulsation hydraulic pressure generating device 23, high-pressure water pipe 24, pressure Transmitter 25.
[0041] The pulsation hydraulic pressure generating devic...
Embodiment 2
[0057] This embodiment is internal high pressure forming with sinusoidal pulsation loading of bulging pressure, combined with Figure 1-7 This embodiment will be described.
[0058] In this embodiment, the internal pressure loading curve function is:
[0059] P 1 (t)=P 0 (t)+ΔPsin(2πωt)
[0060]
[0061] In the formula, ΔP is the pulse wave amplitude, which is 5 MPa in this embodiment; ω is the pulse frequency, which is 1 Hz in this embodiment.
[0062] Compared with Example 1, when the pulsating loading method is selected as 1, the amplitude h needs to be manually measured before the part is formed. Because the system only feeds back and controls the conventional linearly loaded pressure, the pulsating pressure is partially open-loop controlled, and the input program is the amplitude h of the piston rod of the pulsating cylinder, not the amplitude ΔP of the pulsating pressure. Knowing the hydrodynamic properties of the forming medium, the pulsating cylinder, high-pres...
Embodiment 3
[0067] This embodiment is internal high pressure forming with rectangular pulsating loading of bulging pressure, combined with Figure 1-9 , Figure 8 This embodiment will be described.
[0068] In this embodiment, the internal pressure loading curve function is:
[0069]
[0070]
[0071] In the formula, ΔP is the pulse wave amplitude, which is 5 MPa in this embodiment; ω is the pulse frequency, which is 1 Hz in this embodiment.
[0072] Compared with Embodiment 2, the servo motor 49 drives the piston rod 46 to move at the maximum rotational speed in each pulsation period. The piston rod 46 moves quickly from the balance point to the maximum amplitude h, pauses for a period of time, then descends to the position h below the balance point, and quickly returns to the balance point when the pause is the same.
PUM
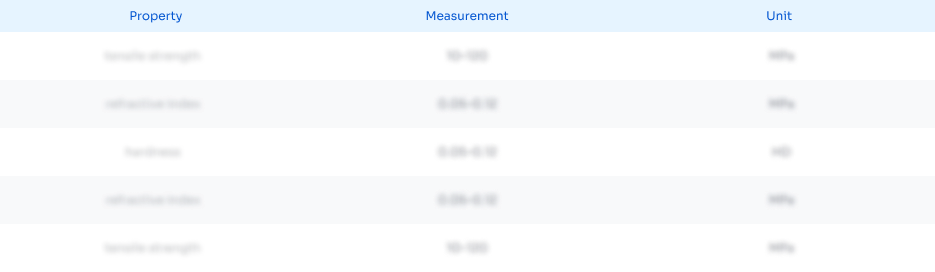
Abstract
Description
Claims
Application Information

- R&D Engineer
- R&D Manager
- IP Professional
- Industry Leading Data Capabilities
- Powerful AI technology
- Patent DNA Extraction
Browse by: Latest US Patents, China's latest patents, Technical Efficacy Thesaurus, Application Domain, Technology Topic, Popular Technical Reports.
© 2024 PatSnap. All rights reserved.Legal|Privacy policy|Modern Slavery Act Transparency Statement|Sitemap|About US| Contact US: help@patsnap.com